Introduction
CFD analysis in pipe flow: The introduction sets the stage for our exploration into the captivating world of Computational Fluid Dynamics (CFD) analysis of pipe flow. Fluid dynamics, a branch of physics and engineering, has always held a certain fascination. It peels back the layers of how liquids and gases move and interact in a myriad of situations. In this section, we embark on a journey to unravel the complexities and intricacies of fluid dynamics, particularly as applied to pipe flow. We’ll see how CFD, a powerful tool in the hands of engineers and researchers, allows us to simulate and understand the behavior of fluids in enclosed conduits. This analytical approach provides insights into various factors affecting flow, from pressure changes to turbulence, and their real-world applications.
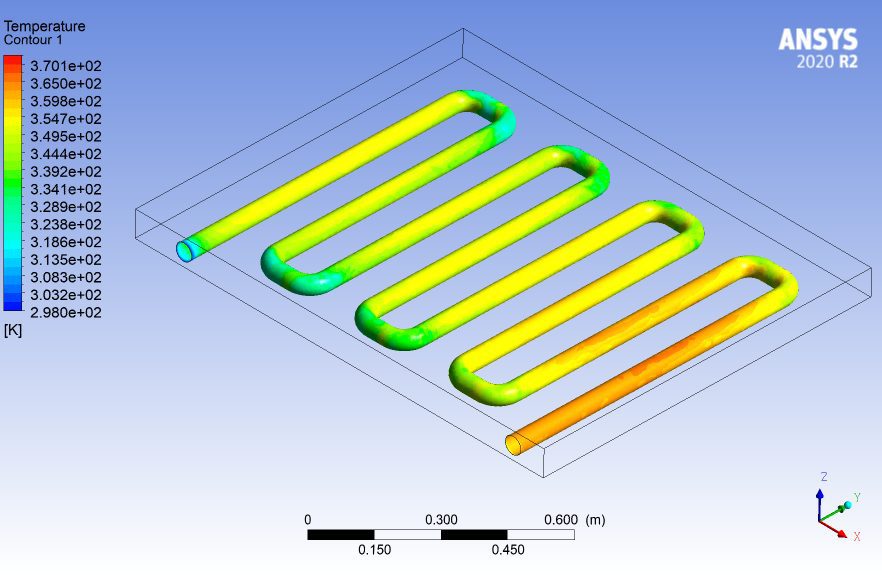
Understanding Pipe Flow
The concept of pipe flow is elemental in fluid dynamics, where it encompasses the movement of liquids or gases within closed pipelines or conduits. In this section, we delve into the core principles and mechanics that govern pipe flow. Understanding this behavior is not merely an academic exercise; it is a fundamental requirement in various industries, including oil and gas, water distribution, and wastewater treatment. When liquids or gases traverse through pipes, they encounter numerous forces, such as pressure gradients, wall friction, and viscosity, all of which contribute to the complex dynamics of pipe flow. By mastering these principles, engineers can design and optimize systems for maximum efficiency and minimal losses.
The Significance of CFD Analysis
Computational Fluid Dynamics (CFD) is the cornerstone of modern engineering and scientific research. In this section, we emphasize the pivotal role that CFD analysis plays in understanding and manipulating fluid dynamics within pipes. It allows us to step into the virtual realm of fluid behavior, facilitating the study of various factors that impact pipe flow. CFD software packages, driven by complex mathematical algorithms, enable engineers and scientists to create detailed simulations of fluid movement, providing a window into the inner workings of a pipeline. With this knowledge, they can optimize designs, troubleshoot problems, and predict system performance, which is indispensable in fields as diverse as aerospace, automotive engineering, and environmental studies.
Setting up the Simulation
As we move further into our exploration, this section introduces us to the practical aspects of conducting a CFD analysis of pipe flow. It all begins with setting up a simulation, a critical step that involves defining the problem, the geometry of the pipe, and the fluid properties. Engineers and researchers must decide what parameters they want to study, whether it’s pressure changes, temperature distribution, or turbulence levels.
Selecting the right software is also essential, as it needs to be capable of handling the complexity of the simulation. The section also discusses the importance of boundary conditions, which mimic the real-world environment, and the initial conditions that define the starting state of the fluid. All of these elements are pivotal in creating a reliable CFD model that can provide accurate insights into pipe flow behavior.
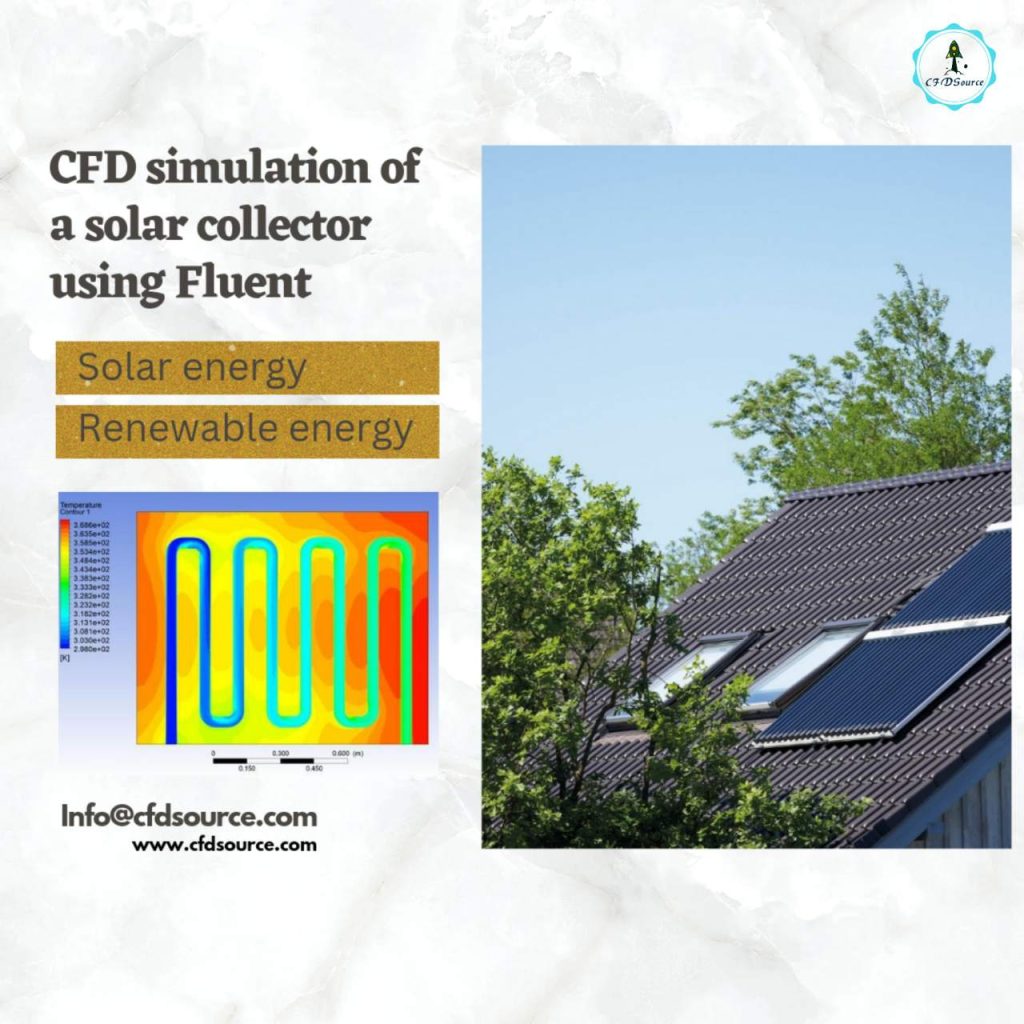
Mesh Generation
Mesh generation is a critical step in Computational Fluid Dynamics (CFD) analysis of pipe flow, and in this section, we delve into its significance. Meshes are the grids that discretize the geometry of the pipe, breaking it down into smaller elements for analysis. The quality and structure of the mesh can greatly impact the accuracy and efficiency of the simulation. Engineers and researchers must strike a balance between having a fine mesh for detailed results and a coarse mesh for faster computations.
Mesh generation involves creating elements like triangles, quadrilaterals, or hexahedra and connecting them to form a grid. This grid is essential for solving the governing equations of fluid dynamics within the pipe. A well-structured mesh ensures that the simulation captures the nuances of the flow, from velocity profiles to pressure gradients, while also allowing for a manageable computational workload.
Solving the Navier-Stokes Equations
The Navier-Stokes equations are the heart of fluid dynamics, and they play a pivotal role in CFD analysis of pipe flow. In this section, we explore the mathematics behind these equations and their importance in understanding fluid behavior within pipes. The Navier-Stokes equations describe the conservation of momentum and the conservation of mass in fluid flow. They account for the various forces acting on the fluid, such as pressure, viscous forces, and gravity.
Solving these equations is no simple task; it requires sophisticated numerical methods and algorithms. CFD software employs iterative techniques to find approximate solutions to these equations, taking into account the mesh generated in the previous step. The resulting solutions provide a detailed view of the flow’s behavior, revealing phenomena like eddies, vortices, and pressure variations. Engineers can analyze this data to optimize designs and make informed decisions about pipe systems.
Post-Processing the Results
Once the CFD simulation is complete, the post-processing of results becomes essential. In this section, we explore the significance of post-processing and how it transforms raw data into actionable insights. The output of a CFD analysis typically includes vast datasets, containing information about velocity, pressure, temperature, and other fluid properties at different points in the pipe. Post-processing involves visualizing and interpreting this data to draw meaningful conclusions.
Engineers use various techniques to create contour plots, vector fields, and streamline patterns, making it easier to grasp the flow behavior. Post-processing also involves calculating performance metrics, such as the coefficient of discharge or pressure drop, which are critical for assessing system efficiency. Through this phase, engineers and researchers can identify areas of improvement, diagnose issues, and fine-tune designs based on the simulation results.
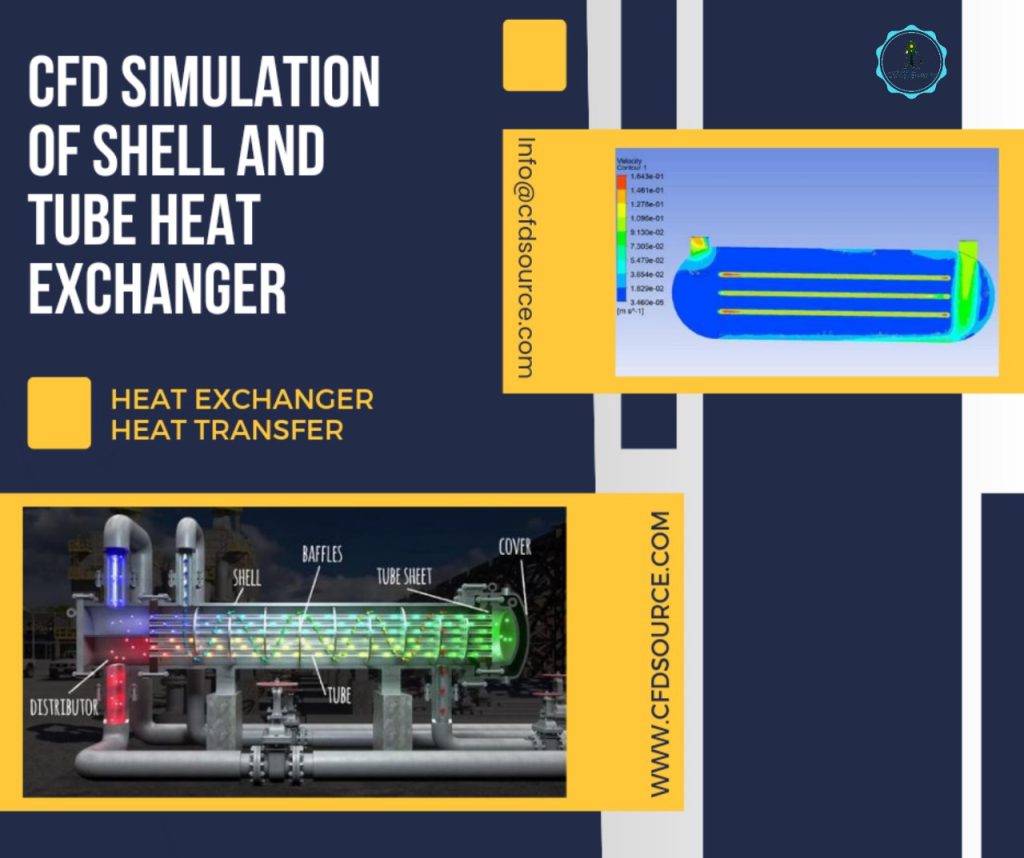
Assessing the Impact of Reynolds Number
The Reynolds number is a dimensionless quantity that holds significant influence over fluid behavior in pipe flow. In this section, we dive into the concept of Reynolds number and its importance in CFD analysis. The Reynolds number is a ratio that compares the inertial forces to the viscous forces within a fluid. It determines whether the flow is laminar or turbulent, and it can significantly affect the behavior of the fluid in the pipe.
For low Reynolds numbers, the flow is typically smooth and predictable (laminar), while high Reynolds numbers lead to chaotic and turbulent flow. Understanding the Reynolds number is crucial for engineers, as it guides their choice of turbulence models and influences design decisions. It’s a key parameter in assessing pipe performance, as it directly impacts factors such as pressure drop and heat transfer. In this section, we explore how engineers calculate and interpret the Reynolds number and discuss its implications in real-world pipe flow scenarios.
Investigating Turbulent Flow
Turbulent flow is a fascinating and complex aspect of fluid dynamics within pipes, and in this section, we take a closer look at this phenomenon. When the Reynolds number is sufficiently high, fluid flow becomes turbulent, characterized by chaotic, swirling motion. Turbulence is a challenge in many engineering applications, as it leads to increased pressure drop, heat transfer, and energy losses. Understanding and managing turbulent flow are crucial for optimizing pipe systems.
Engineers and researchers utilize CFD analysis to investigate turbulence by simulating its behavior within a pipe. They can analyze turbulence intensity, turbulent kinetic energy, and the dissipation rate to gain insights into flow patterns. This knowledge is invaluable for designing systems that mitigate the negative effects of turbulence, such as using flow control devices or altering pipe geometries to promote laminar flow in critical areas.
Heat Transfer Analysis
Heat transfer plays a vital role in pipe flow systems, and in this section, we explore its significance. Pipes are not only conduits for transporting fluids but also for transferring heat. Heat transfer analysis is essential in applications like heating, cooling, and thermal energy transport. CFD analysis allows engineers to investigate the temperature distribution within pipes and how it evolves as the fluid flows. This analysis considers various heat transfer mechanisms, including conduction, convection, and radiation.
By understanding these processes, engineers can optimize heat exchangers, design efficient heating or cooling systems, and address temperature-related issues such as overheating or freezing. Furthermore, CFD simulations provide a detailed view of thermal behavior, enabling engineers to make informed decisions about insulation, material selection, and heat management strategies.
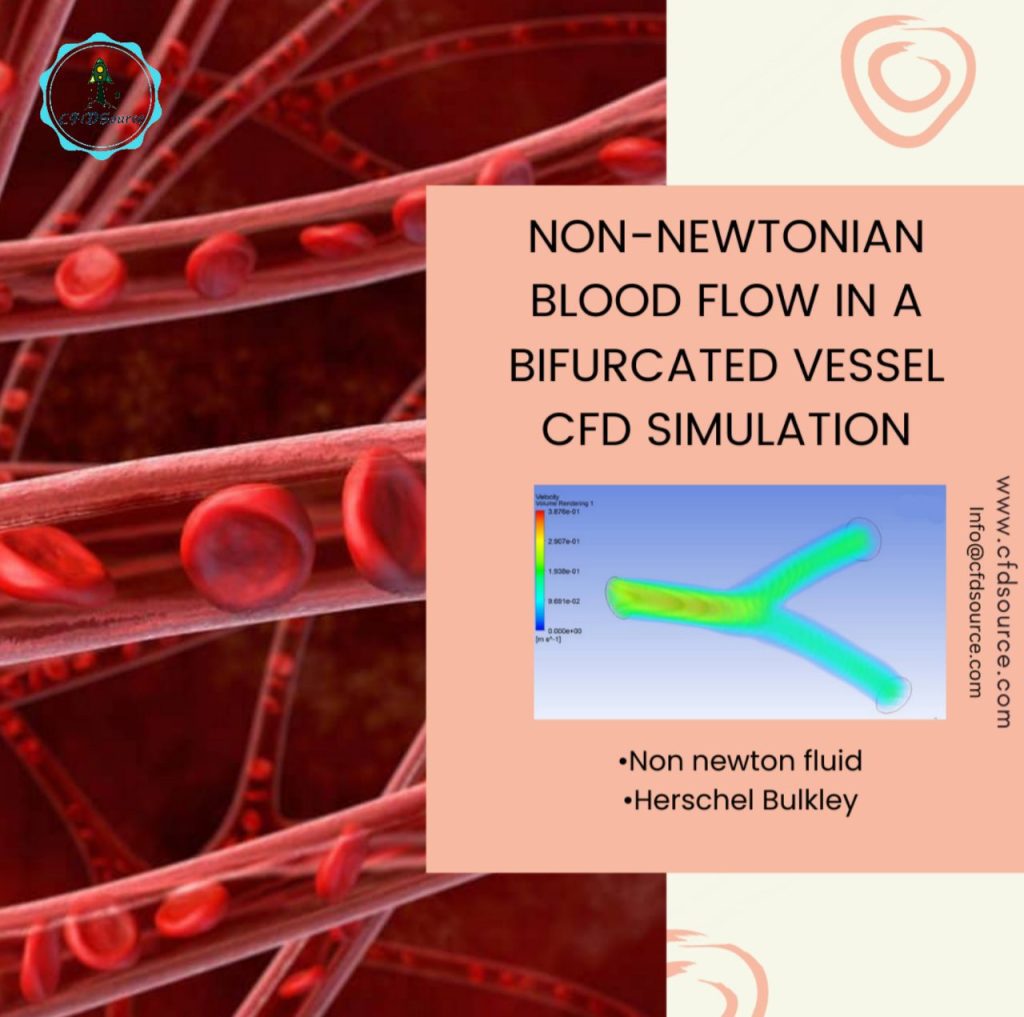
Applications in Industry
In this section, we delve into the diverse range of applications of CFD analysis of pipe flow across different industries. CFD has become a fundamental tool in engineering and scientific research, and its applications in the context of pipe flow are vast. In the oil and gas industry, CFD is used to optimize the design of pipelines and predict the behavior of multiphase flow, ensuring the efficient transport of hydrocarbons. In water distribution systems, CFD helps engineers design pipe networks that deliver water with minimal losses and energy consumption.
The pharmaceutical industry uses CFD to understand drug mixing and heat transfer processes in pipes. Aerospace and automotive engineering leverage CFD to optimize fuel injection and cooling systems. Environmental studies use CFD to model pollutant dispersion in air and water. The applications are virtually limitless, and this section provides a glimpse into how CFD enhances efficiency and innovation in various sectors.
Challenges and Limitations
While CFD analysis of pipe flow offers tremendous benefits, it’s not without challenges and limitations, as discussed in this section. One significant challenge is the computational resources required for complex simulations. High-resolution meshes and detailed simulations demand substantial computing power and time. Another challenge is the accuracy of the results. CFD models make simplifications and assumptions, and the reliability of the simulation depends on how well these assumptions match the real-world scenario. Additionally, turbulence modeling is still an evolving field, and predicting turbulent flow accurately can be challenging.
The limitations of CFD also include the need for expertise in setting up simulations and interpreting results. Engineers and researchers must have a deep understanding of both the software and the physics involved. Furthermore, CFD cannot always capture transient or unsteady phenomena, and it may struggle with highly complex geometries. Recognizing these challenges and limitations is essential for ensuring that CFD analysis is applied appropriately and its results are interpreted accurately.
Advancements in CFD Technology
In the world of Computational Fluid Dynamics (CFD), technology is continually evolving, and this section delves into the exciting advancements that are shaping the field. CFD software and techniques have come a long way, enabling engineers and researchers to perform more complex and accurate simulations. High-performance computing has become more accessible, allowing for faster simulations with finer mesh resolutions. The advent of cloud computing has also made it easier for organizations to tap into significant computational power.
Additionally, there have been advancements in turbulence modeling, with the development of improved turbulence models and hybrid approaches that better capture the intricacies of turbulent flow. Machine learning and artificial intelligence are being integrated into CFD to enhance automation, optimization, and predictive capabilities. Furthermore, CFD is moving towards more interdisciplinary applications, combining fluid dynamics with structural analysis and heat transfer for a more holistic approach to engineering problems. These advancements open new horizons for CFD, making it an indispensable tool for innovation and problem-solving in various industries.
Conclusion
In this section, we conclude our journey through the fascinating realm of CFD analysis of pipe flow. We have explored the fundamental principles of fluid dynamics within pipes, the significance of CFD analysis, and the various steps involved in the process. From setting up simulations to post-processing results and assessing the impact of the Reynolds number, we’ve unveiled the intricacies of pipe flow behavior. We’ve discussed turbulent flow, heat transfer analysis, and the wide-ranging applications of CFD across diverse industries. It’s evident that CFD is not just a scientific discipline but a powerful tool that empowers engineers and researchers to optimize designs, troubleshoot issues, and drive innovation. However, we’ve also touched upon the challenges and limitations of CFD, emphasizing the importance of using this tool judiciously. As we conclude, it’s clear that the world of fluid dynamics is both a captivating and complex domain, and CFD is the key that unlocks its secrets.