CFD Analysis of Aircraft Wing: Computational Fluid Dynamics (CFD) has become an indispensable tool in the field of aerospace engineering, particularly in the analysis and design of aircraft wings. This essay will delve into the intricacies of CFD analysis for aircraft wings, exploring the techniques, applications, challenges, and future prospects of this critical aspect of aviation.
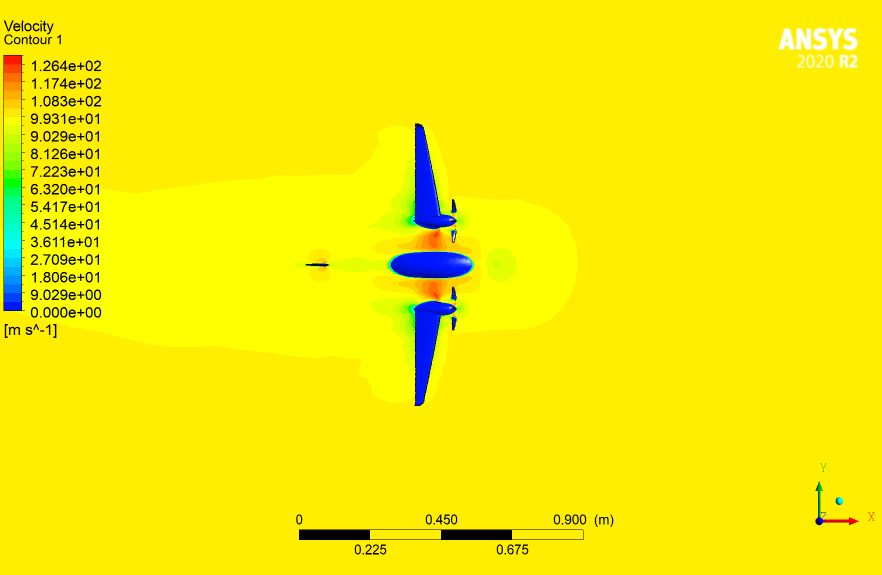
1. Introduction to CFD Analysis of Aircraft Wing
Aircraft wings are the unsung heroes of the aviation world, bearing the weight of an entire aircraft and ensuring it takes to the skies. But beneath their seemingly simple design lies a world of complexity. The study and analysis of aircraft wings have evolved significantly with the advent of Computational Fluid Dynamics, or CFD. CFD analysis is the scientific art of simulating airflow around these crucial components to understand their aerodynamic behavior.
In this age of technological advancement, it’s no longer sufficient to rely solely on wind tunnels and physical experiments. CFD has become the backbone of optimizing wing design, ensuring aircraft safety, and enhancing performance. This essay explores the fascinating world of CFD analysis of aircraft wings, delving deep into the science that keeps airplanes aloft.
2. Understanding Computational Fluid Dynamics (CFD)
To truly grasp the significance of CFD in aircraft wing analysis, we must first understand the essence of Computational Fluid Dynamics itself. At its core, CFD is a numerical technique used to solve the Navier-Stokes equations, which describe fluid flow. In the context of aircraft wings, this technique is applied to model and predict how air flows around and interacts with these critical components. The power of CFD lies in its ability to simulate fluid flow without the need for physical prototypes.
Engineers use CFD software to create a virtual environment in which they can test different wing designs and configurations. This saves both time and resources, as it eliminates the necessity of costly wind tunnel experiments. In essence, CFD allows us to ‘see’ the invisible – the behavior of air as it swirls around an aircraft wing.
3. The Importance of Aircraft Wing Design
Aircraft wing design is not merely about aesthetics; it’s a science that directly influences the fundamental principles of aviation. An aircraft’s wings are not static objects; they are dynamic, performing a delicate dance with the air to generate lift and minimize drag. The importance of optimizing wing design cannot be overstated. Efficient wing design is the key to achieving the perfect balance between lift, which keeps an aircraft aloft, and drag, which resists its forward motion. The quest for optimal wing design is driven by the desire for better fuel efficiency, safety, and overall performance. This is where CFD analysis comes into play. By simulating the behavior of air around various wing shapes, engineers can fine-tune wing designs to minimize drag, maximize lift, and ensure safe and efficient flight.
4. Applications of CFD in Aerospace Engineering
The applications of CFD in aerospace engineering are both extensive and diverse. CFD is the linchpin that connects theoretical aerodynamics to practical aviation engineering. Beyond aircraft wings, CFD plays a vital role in designing and analyzing various components of aircraft, including engines, fuselages, and even the entire aircraft structure. It is the ultimate tool for understanding how aerodynamic forces act upon an aircraft, influencing every aspect of its design and operation.
In modern aerospace engineering, CFD is involved from the conceptual stage of a new aircraft’s design to fine-tuning existing models. It enables engineers to conduct a range of analyses, from studying the airflow around the aircraft’s body to evaluating the performance of its engines. In short, CFD is the key to achieving safe, efficient, and high-performance aircraft, making it indispensable in the aerospace industry.
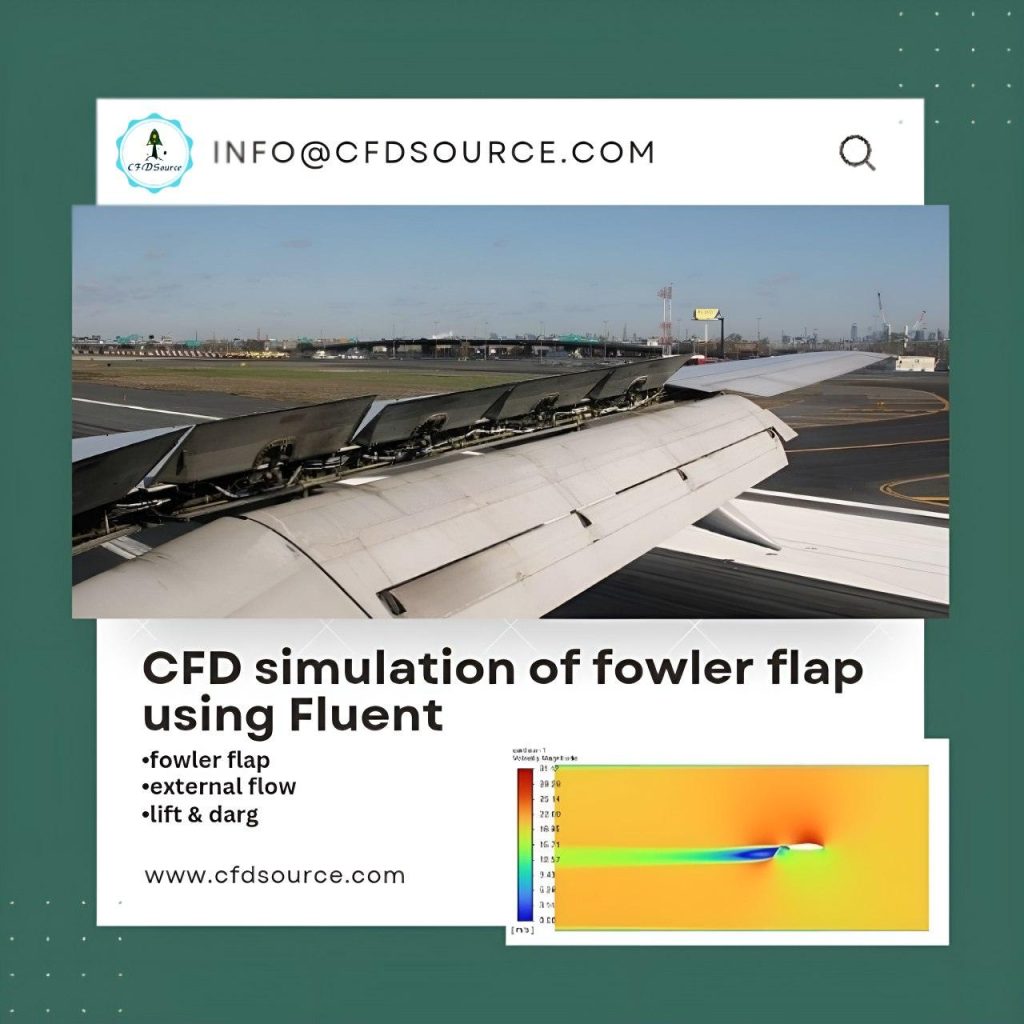
5. Steps in Conducting a CFD Analysis for Aircraft Wings
The process of conducting a CFD analysis for aircraft wings is a well-defined and systematic journey, consisting of several crucial steps. The first step, preprocessing, involves defining the geometry of the wing and setting up simulation parameters. Engineers create a digital representation of the wing, specifying its dimensions, shape, and the surrounding environment. Once the groundwork is laid, it’s time for mesh generation, a critical phase in CFD analysis. Here, a grid, or mesh, is created to discretize the domain around the wing into smaller elements.
This grid is instrumental in solving the complex equations governing fluid flow. With the mesh in place, the heart of CFD analysis begins—solving the Navier-Stokes equations. This is where the magic happens; mathematical equations representing fluid flow are solved in a virtual space, and the behavior of air around the wing is simulated. Finally, the results are post-processed, meaning they are interpreted and visualized to extract valuable information. These steps may sound straightforward, but they require a deep understanding of mathematics, physics, and computational techniques, making CFD analysis a specialized field within aerospace engineering.
6. Key Parameters Analyzed in CFD Simulations
A CFD simulation for aircraft wings isn’t just about pretty visualizations; it’s a data-rich process that provides engineers with a wealth of information. Three key parameters take the spotlight in CFD simulations: lift and drag coefficients, pressure distribution, and flow velocity. Lift and drag coefficients are fundamental in aviation. They provide a quantitative measure of how effectively a wing generates lift (the force that opposes gravity and keeps the aircraft airborne) and how much drag it produces (the force that resists forward motion).
By optimizing these coefficients, engineers can make aircraft more fuel-efficient, ensuring they require less power to stay in the air. Pressure distribution analysis is equally crucial. It reveals how air pressure varies across the wing’s surface. Understanding these pressure variations is vital for maintaining structural integrity and enhancing aerodynamic performance. Flow velocity, the third parameter, allows engineers to see how air moves around the wing. It helps in identifying areas of potential turbulence and optimizing airflow for efficiency. Together, these parameters provide a comprehensive view of how the wing performs in various flight conditions.
7. Challenges in CFD Analysis of Aircraft Wings
While CFD analysis offers incredible insights into aircraft wing behavior, it’s not without its challenges. Two major hurdles engineers face in this field are turbulence modeling and validation and verification. Turbulence, the seemingly chaotic movement of fluids, is notoriously difficult to model accurately. Within the boundary layer of an aircraft wing, turbulent flow can drastically affect lift, drag, and even structural integrity. CFD software must simulate these turbulent flows as closely as possible to provide reliable results. Validation and verification pose another conundrum.
Engineers need to ensure that the CFD simulations match real-world observations. This requires extensive testing and validation experiments in wind tunnels or flight tests. Overcoming these challenges involves a combination of sophisticated mathematical models, computational power, and meticulous validation processes, ensuring that CFD remains a credible and reliable tool in aerospace engineering.
8. Advancements in CFD Technology
Advancements in CFD technology have propelled aerospace engineering into a new era of design and analysis. Historically, CFD simulations were computationally intensive and time-consuming, limiting their application. However, modern computing power has revolutionized the field. With faster processors and parallel computing, engineers can now conduct simulations in a fraction of the time it once took. Furthermore, the accuracy of simulations has improved dramatically due to refined mathematical models and more precise boundary conditions.
The development of high-fidelity turbulence models has made it possible to represent turbulence with greater accuracy, a longstanding challenge in CFD. Parallel to hardware advancements, CFD software has evolved as well, offering user-friendly interfaces and robust features that facilitate the entire analysis process. These advancements have democratized CFD, making it more accessible to smaller aerospace firms and research institutions. As CFD technology continues to evolve, it opens doors to innovative and ambitious aircraft designs, ensuring the industry keeps pushing the boundaries of what’s possible in aviation.
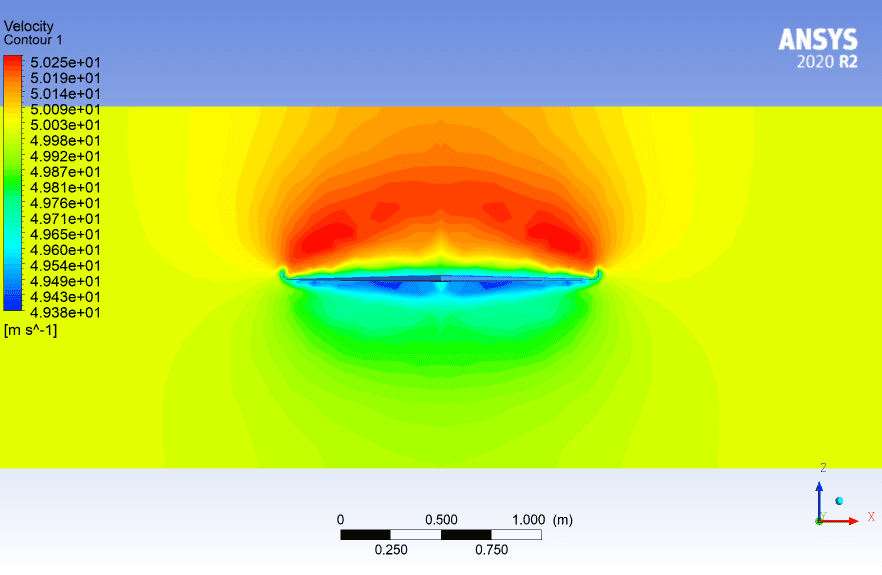
9. Real-Life Examples of CFD Analysis in Aircraft Wing Design
Real-life examples of CFD analysis in aircraft wing design abound, showcasing the tangible benefits of this technology in the aerospace industry. Consider the case of the Boeing 787 Dreamliner. Boeing employed CFD simulations extensively during its development to optimize the Dreamliner’s advanced aerodynamics. The result was a fuel-efficient, long-haul aircraft that fundamentally transformed air travel. Another example is the Airbus A350 XWB, a marvel of modern aviation engineering.
Airbus utilized CFD analysis to create a highly efficient wing design, reducing drag and improving overall performance. The wings of the A350 are meticulously sculpted to maximize lift while minimizing fuel consumption. These real-world applications of CFD illustrate how this technology is indispensable for crafting next-generation aircraft that are more eco-friendly and cost-effective.
10. Future Trends in CFD Analysis for Aircraft Wings
As technology and engineering continue to advance, so too does the field of CFD analysis for aircraft wings. One promising trend is the growing use of artificial intelligence and machine learning to enhance CFD simulations. These technologies can optimize mesh generation, improve turbulence modeling, and accelerate the analysis process. Additionally, the integration of CFD with other engineering disciplines, such as structural analysis and materials science, will become more prevalent.
This holistic approach will allow engineers to design wings that not only perform optimally but are also structurally sound and lightweight. Furthermore, CFD will play a crucial role in the development of electric and hybrid-electric aircraft, as aerodynamics become even more critical for maximizing efficiency and range. With advancements in computational power, CFD will continue to refine its ability to predict real-world behaviors with greater accuracy, ensuring aircraft wings remain at the forefront of innovation in aviation.
11. Conclusion
In conclusion, the realm of Computational Fluid Dynamics (CFD) analysis for aircraft wings is a dynamic and indispensable field within aerospace engineering. It enables engineers to delve deep into the intricacies of aerodynamics and create wings that are efficient, safe, and high-performing. From the early stages of geometry definition to the final post-processing of simulation results, CFD analysis is a well-structured process that saves time and resources compared to traditional wind tunnel experiments. It has played a pivotal role in the development of iconic aircraft like the Boeing 787 Dreamliner and the Airbus A350 XWB, ushering in a new era of aviation. However, CFD analysis is not without its challenges, particularly in modeling turbulence and validating results.
CFD Analysis of Aircraft Wing: These challenges are met with ongoing technological advancements, both in hardware and software, making CFD increasingly accessible and powerful. As we look to the future, CFD’s integration with artificial intelligence, its role in electric aviation, and its potential to transform aircraft design indicate a bright future for this technology. The aerodynamic efficiency of aircraft wings will continue to evolve, ensuring safer, greener, and more efficient air travel for generations to come.