CFD Analysis of Centrifugal Fan: Centrifugal fans play a vital role in various industrial applications, from HVAC systems to manufacturing processes. These devices are designed to move air or gases and are widely used in ventilation, cooling, and material handling systems. To ensure the optimal performance of centrifugal fans, engineers turn to Computational Fluid Dynamics (CFD) analysis, a sophisticated and powerful tool for evaluating their efficiency and performance.
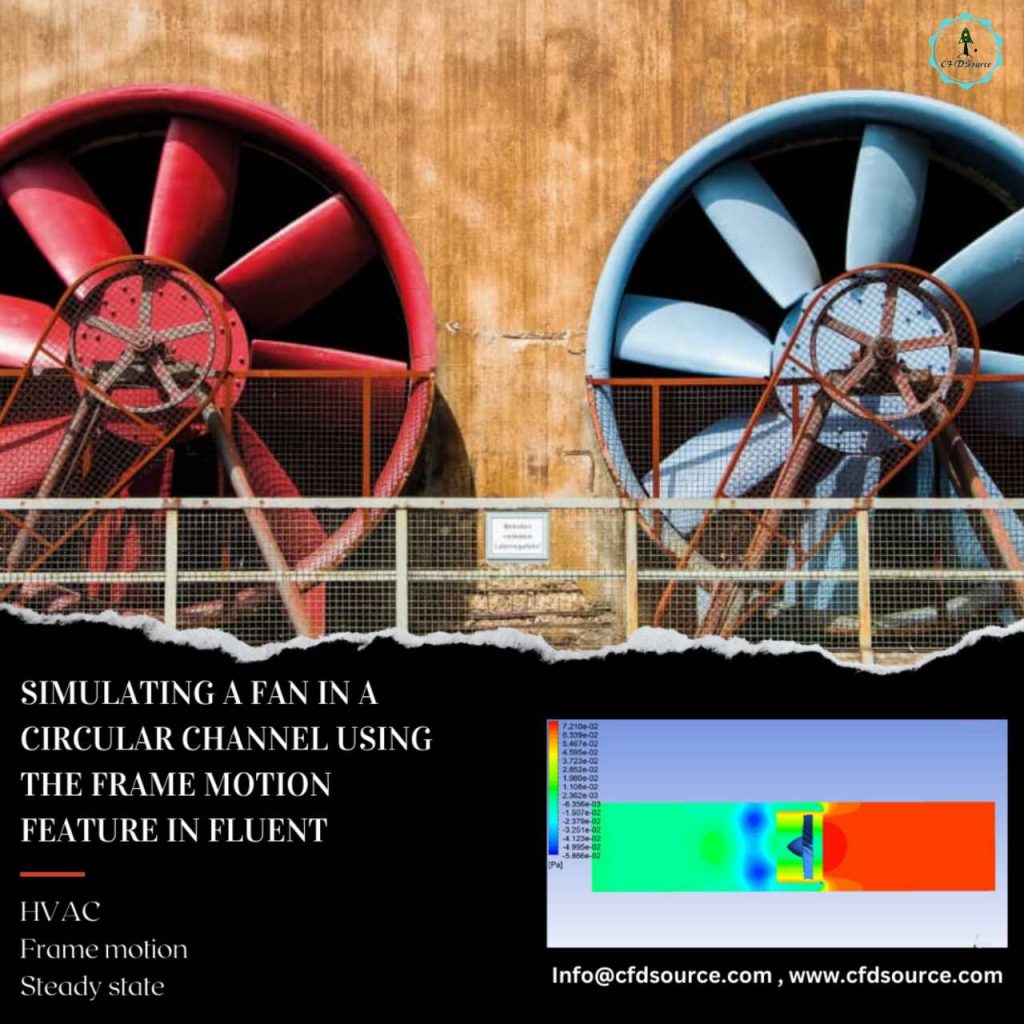
Introduction to CFD Analysis
Computational Fluid Dynamics (CFD) analysis is a powerful and versatile tool in the field of engineering and design. It is a computer-based technique that allows engineers and scientists to simulate and analyze the behavior of fluid flows in various settings. Whether it’s studying the aerodynamics of an aircraft, optimizing the cooling system in a data center, or even evaluating the performance of a centrifugal fan, CFD analysis is indispensable. The primary purpose of CFD is to gain insights into how fluids, such as air or liquids, behave under different conditions. This includes examining flow patterns, pressure distributions, and temperature variations within a given environment. In essence, CFD analysis helps us understand the complex dynamics of fluid flow, allowing us to make informed decisions and improvements in various engineering applications.
Understanding Centrifugal Fans
Centrifugal fans are fascinating devices that are integral to numerous industrial and commercial applications. They consist of an impeller with blades that rotate, generating a centrifugal force that drives the movement of air or gases. What makes centrifugal fans distinct is their ability to produce high-pressure, low-volume airflow. This characteristic is particularly useful in scenarios where efficient ventilation, cooling, or material handling is required. Centrifugal fans are commonly found in heating, ventilation, and air conditioning (HVAC) systems, as well as in industrial processes like material transportation and dust collection. Understanding the basic principles of how centrifugal fans operate is vital to grasp their significance and the role CFD analysis plays in optimizing their performance.
Importance of CFD Analysis in Fan Design
The importance of CFD analysis in fan design cannot be overstated. The performance of a centrifugal fan depends on several design parameters, such as the impeller’s blade shape, the size of the impeller, and the configuration of the fan housing. These factors directly impact airflow patterns, pressure differentials, and energy efficiency. CFD analysis serves as a virtual testing ground, allowing engineers to manipulate these parameters and observe the resulting effects on fan performance.
This capability is invaluable for optimizing fan designs to meet specific requirements. By leveraging CFD, engineers can ensure that the fans they design and use are not only energy-efficient but also capable of delivering precise airflow and pressure, which is vital in many industrial and commercial processes. In essence, CFD analysis empowers engineers to fine-tune the design of centrifugal fans to enhance their overall performance and functionality.
The Working Principle of Centrifugal Fans
To appreciate the role of CFD analysis in optimizing centrifugal fans, it’s essential to understand the fundamental principles behind how these fans work. The key component of a centrifugal fan is the impeller, a rotating disk with blades that capture and accelerate the air. As the impeller rotates, it creates a centrifugal force that pushes the air radially outward. This outward movement of air generates a high-velocity airflow, which is directed into a diffuser.
Within the diffuser, the kinetic energy of the air is converted into pressure energy. This transformation of energy is what enables the fan to generate the necessary airflow and pressure required for various applications. The ability to control and enhance this energy transformation is where CFD analysis becomes invaluable. It allows engineers to precisely model and understand how the air behaves within the fan, which is crucial for optimizing fan efficiency and performance.
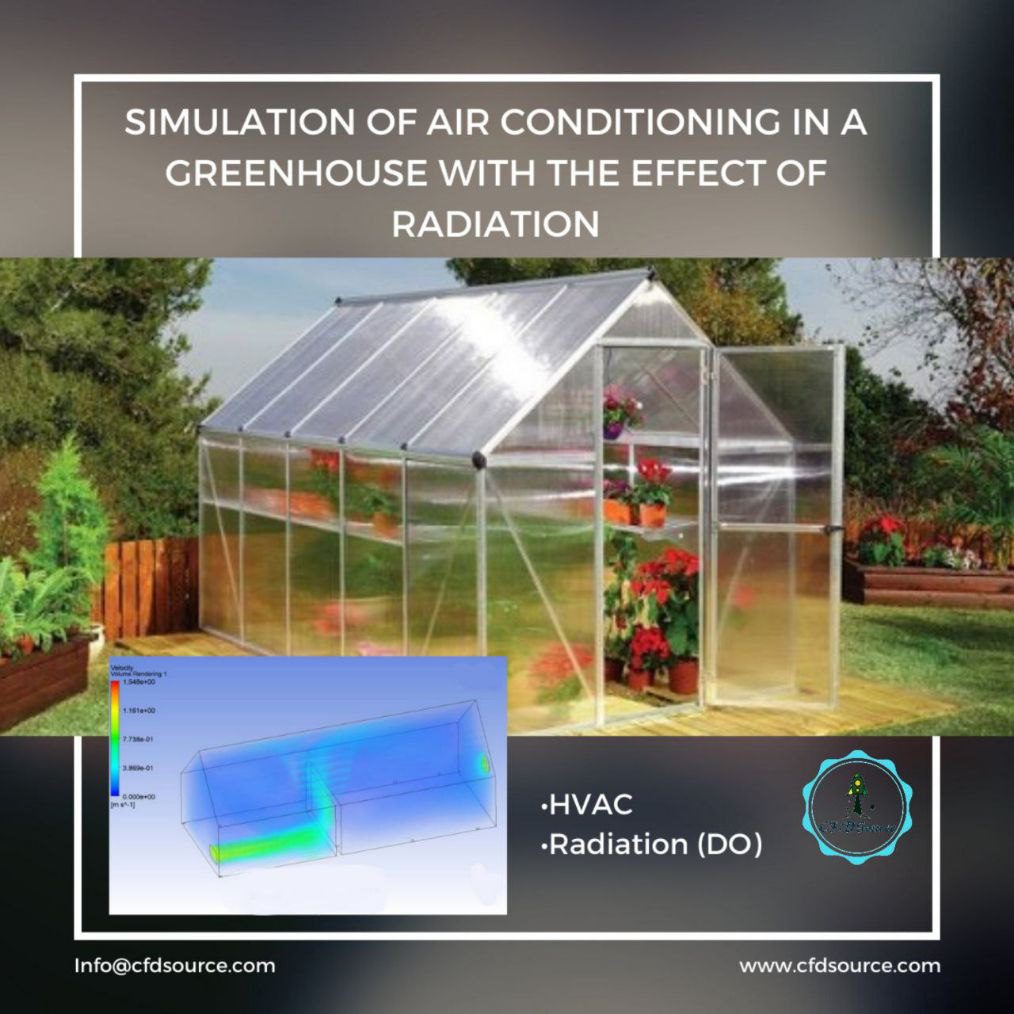
Steps in Conducting CFD Analysis
Conducting Computational Fluid Dynamics (CFD) analysis is a systematic and multi-faceted process that serves as the cornerstone of optimizing centrifugal fan performance. This journey begins with data gathering. Accurate and comprehensive data collection is the bedrock upon which the entire analysis rests. It encompasses aspects like the fan’s dimensions, materials, operating environment, and performance goals. Without reliable data, the CFD analysis would lack the foundation needed to produce meaningful results.
The next step in this journey is the creation of a 3D digital model of the centrifugal fan. This digital twin must be a faithful and precise representation of the physical fan, including all of its components – the impeller, housing, and any additional structures. The accuracy of this model is vital as any discrepancies will be reflected in the CFD analysis, potentially leading to inaccurate conclusions.
Mesh generation is the following step, where the 3D model is divided into smaller elements or cells. The quality and size of the mesh directly impact the CFD analysis. Finer meshes provide higher accuracy but require more computational resources. Engineers must strike a balance to ensure the simulation is both accurate and computationally manageable.
Setting boundary conditions is the next pivotal step. In this phase, engineers define the conditions at the inlet and outlet of the computational domain to replicate real-world scenarios. The inlet conditions are of particular importance, as they dictate the characteristics of the air entering the fan. Accurate boundary conditions ensure the simulation mirrors the actual working conditions and thereby provides realistic insights.
With data gathered, the 3D model created, the mesh generated, and boundary conditions set, it’s time for the CFD software to run the simulation. This phase involves solving the Navier-Stokes equations and other governing equations of fluid dynamics within the fan’s computational domain. This detailed computation accounts for the airflow patterns, pressure gradients, and temperature distributions. It’s a computationally intensive process that may necessitate high-performance computing resources. However, it’s in this phase that the magic happens, as the software reveals how air moves through the fan, offering insights into performance and efficiency.
Gathering Data for Analysis
The process of conducting Computational Fluid Dynamics (CFD) analysis begins with the collection of comprehensive and accurate data. This foundational step is essential to ensure the CFD analysis is based on real-world parameters, enabling engineers to make informed decisions. The data collected encompasses various aspects of the centrifugal fan, including its physical dimensions, materials, and structural characteristics. Additionally, information about the operating environment is critical, covering factors such as temperature, pressure, humidity, and the intended performance goals of the fan. The quality and reliability of this data significantly impact the accuracy of the subsequent CFD analysis. Engineers must be meticulous in their data collection to ensure that the simulation accurately mirrors the fan’s actual behavior.
Creating the 3D Model
Following the meticulous data gathering, the next critical step in conducting CFD analysis is the creation of a 3D digital model of the centrifugal fan. This digital twin serves as the virtual representation of the physical fan, including all its components, such as the impeller, housing, and any additional features. The precision and accuracy of this model are paramount. It must faithfully reproduce the fan’s geometry and structure to ensure that the CFD analysis closely mirrors the real-world conditions. Engineers utilize specialized software to generate this 3D model, meticulously defining every aspect of the fan’s design. Creating an accurate 3D model is vital to ensure that the simulation results are meaningful and can be effectively used for performance optimization.
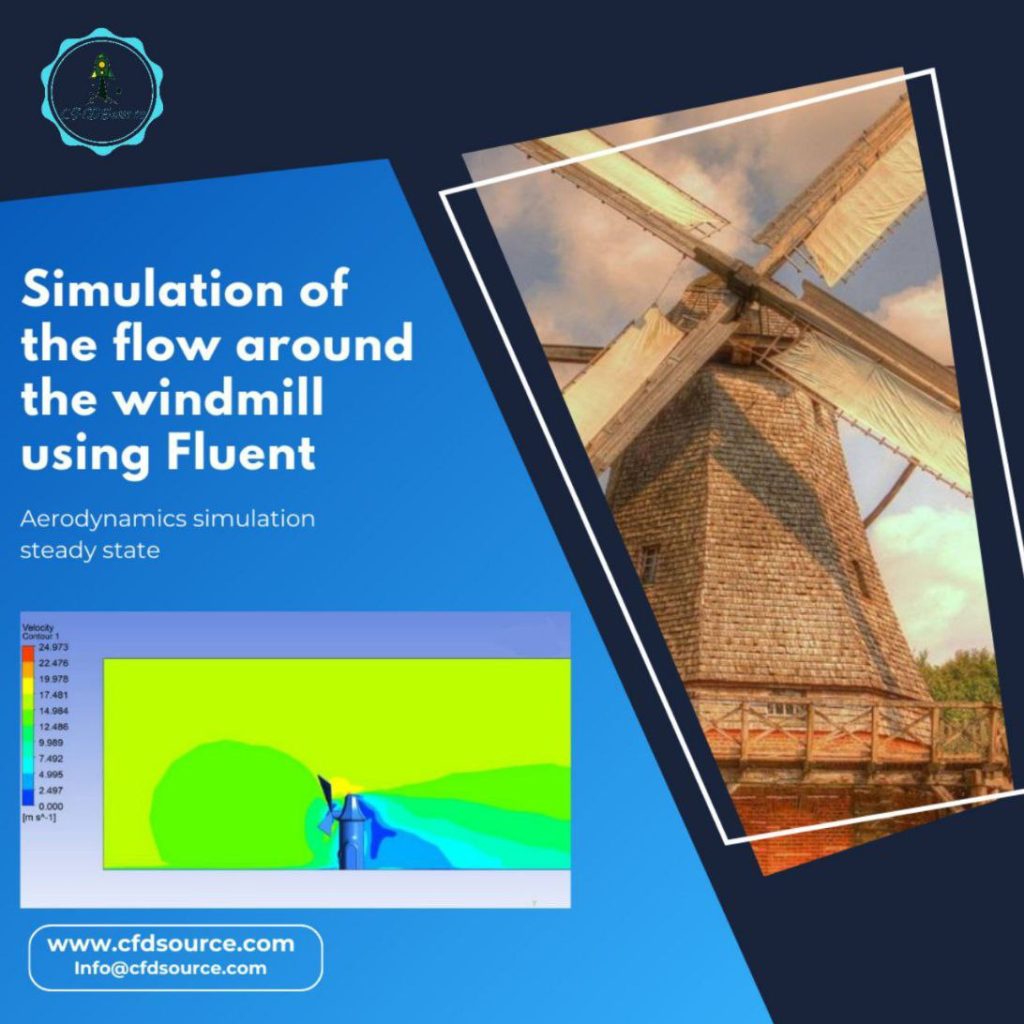
Mesh Generation for Accurate Results
With the 3D model in place, the subsequent step in the CFD analysis process is mesh generation. Meshing is the process of dividing the 3D model into smaller elements or cells, effectively creating a grid. The size and quality of the mesh have a direct impact on the precision and efficiency of the CFD analysis. Engineers need to strike a balance between a fine mesh that provides highly accurate results and a coarser mesh that demands fewer computational resources.
The key challenge is to ensure that the mesh captures the complex flow patterns, turbulence, and variations in airflow within the centrifugal fan accurately. Proper mesh generation is crucial for the reliability of the simulation, as it influences the ability to capture fine details within the fan’s operation. It is a process that requires expertise and careful consideration to ensure that the CFD analysis yields the desired level of accuracy and efficiency.
Setting Boundary Conditions
Setting precise boundary conditions is a fundamental aspect of conducting Computational Fluid Dynamics (CFD) analysis for centrifugal fans. These conditions define the parameters at the inlet and outlet of the fan’s computational domain, thereby simulating real-world operating scenarios. In the context of centrifugal fans, the inlet boundary conditions are particularly critical. Engineers must accurately specify factors such as air velocity, temperature, and pressure at the fan’s inlet to replicate the actual working environment.
These conditions are what drive the flow of air through the fan. Furthermore, it’s essential to establish the correct outlet conditions, as they dictate how the air exits the fan. Properly defined boundary conditions are vital for obtaining meaningful results from the CFD analysis, as they ensure the simulation accurately mimics the fan’s behavior under different operating conditions.
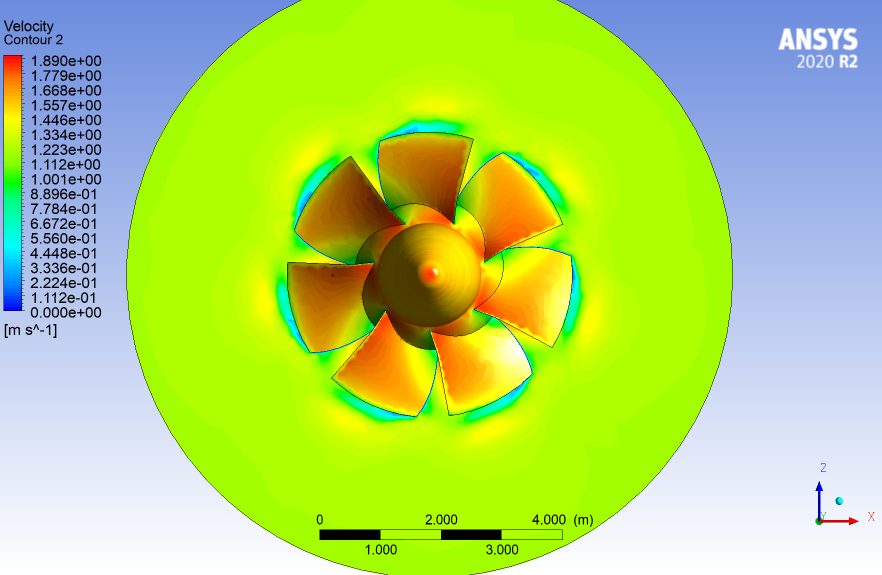
Running the Simulation
Running the simulation is the heart of any Computational Fluid Dynamics (CFD) analysis. This is where the CFD software takes over and conducts the complex calculations that model fluid flow within the centrifugal fan. At this stage, the software solves the governing equations of fluid dynamics, typically the Navier-Stokes equations, within the fan’s defined geometry and under the set boundary conditions. The software divides the fan’s computational domain into a mesh of cells and computes how air moves through them.
This process encompasses the simulation of various factors, including airflow patterns, pressure gradients, and temperature distributions. The accuracy of the results relies on the precise representation of the fan’s geometry and the fidelity of the boundary conditions. Depending on the complexity of the model and the desired level of detail, running the simulation can be computationally intensive, often requiring high-performance computing resources to ensure efficient and accurate results.
Analyzing Results
The analysis of results is the stage where the raw data generated by the Computational Fluid Dynamics (CFD) simulation is transformed into meaningful insights. After a simulation run, engineers are confronted with vast datasets that encompass everything from velocity vectors to pressure contours. Analyzing this wealth of information is a critical step in the CFD analysis process. Engineers employ a variety of visualization tools and post-processing techniques to make sense of the data.
They look for flow patterns and turbulence, identifying areas of interest and evaluating the fan’s performance under different conditions. Through this analysis, engineers can pinpoint regions of high and low pressure, identify potential areas of energy loss or turbulence, and understand how the fan’s design influences its performance. It’s the analysis phase that provides the crucial information needed to make informed decisions about optimizing the fan’s efficiency and performance.
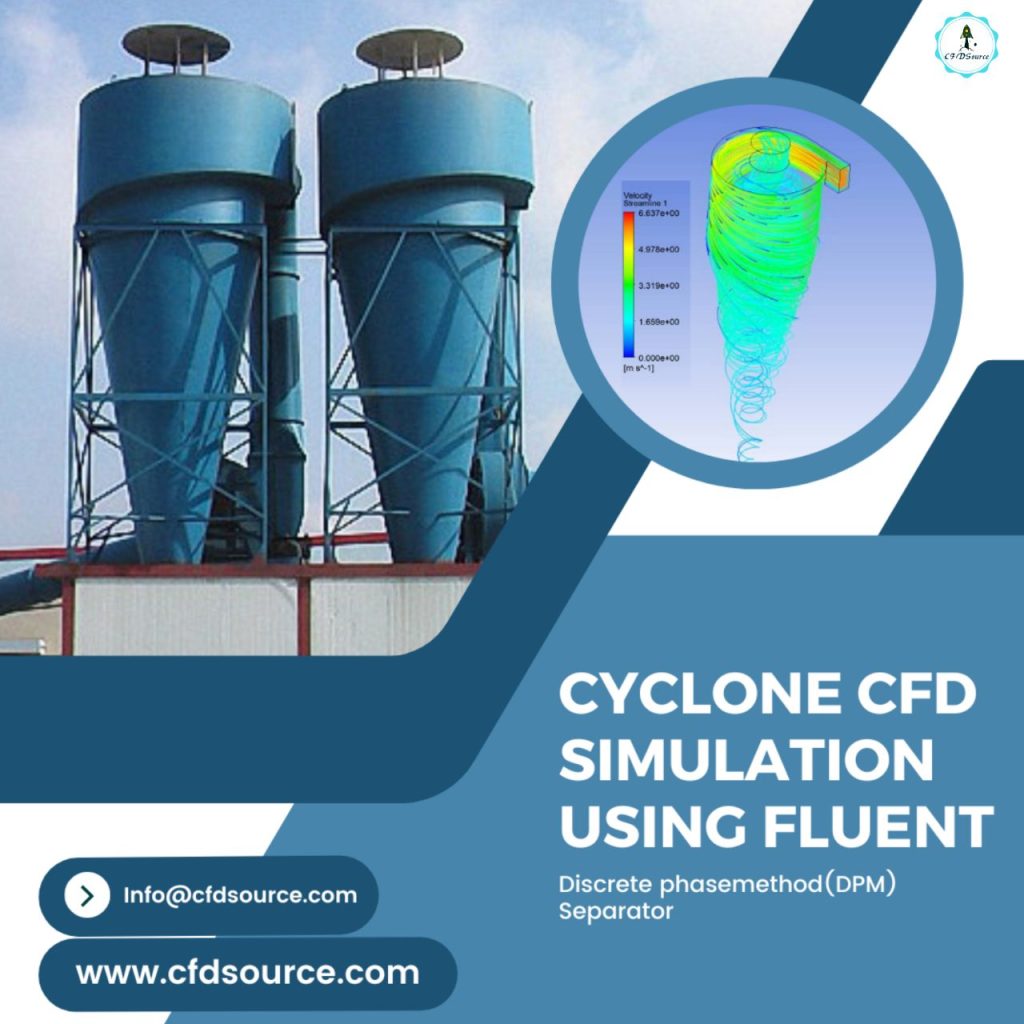
Conclusion
CFD Analysis of Centrifugal Fan: In conclusion, Computational Fluid Dynamics (CFD) analysis plays a pivotal role in the design and optimization of centrifugal fans and various other engineering applications. It offers a powerful means to simulate and analyze fluid flow behavior, providing critical insights that enable engineers to make informed decisions regarding design modifications and performance enhancements. By carefully following the systematic steps of CFD analysis, from data gathering to result analysis, engineers can ensure the reliability and accuracy of their simulations. Despite the challenges it presents, including the need for specialized software and hardware, precise data collection, meshing considerations, and boundary condition definition, CFD analysis remains an indispensable tool in a multitude of industries.
Whether in the design of efficient HVAC systems, aerospace engineering, automotive manufacturing, petrochemical processes, or electronics cooling, CFD analysis contributes to improved performance, energy efficiency, and safety. It is not just a technical tool but a catalyst for innovation and progress in engineering and design. The power of CFD analysis lies in its ability to bridge the gap between theory and real-world application, providing engineers with the means to create more efficient, cost-effective, and sustainable solutions for the complex challenges of our modern world. In a world driven by technology and innovation, CFD analysis is a key driver of progress, enabling us to design systems that are not only functional but also environmentally conscious and economically sustainable.