CFD analysis of double pipe heat exchanger: In the world of heat transfer and thermodynamics, the analysis and optimization of heat exchangers play a pivotal role in ensuring energy efficiency and cost-effectiveness. One of the techniques employed in this endeavor is Computational Fluid Dynamics (CFD) analysis. This essay explores the significance of CFD analysis in the context of double pipe heat exchangers.
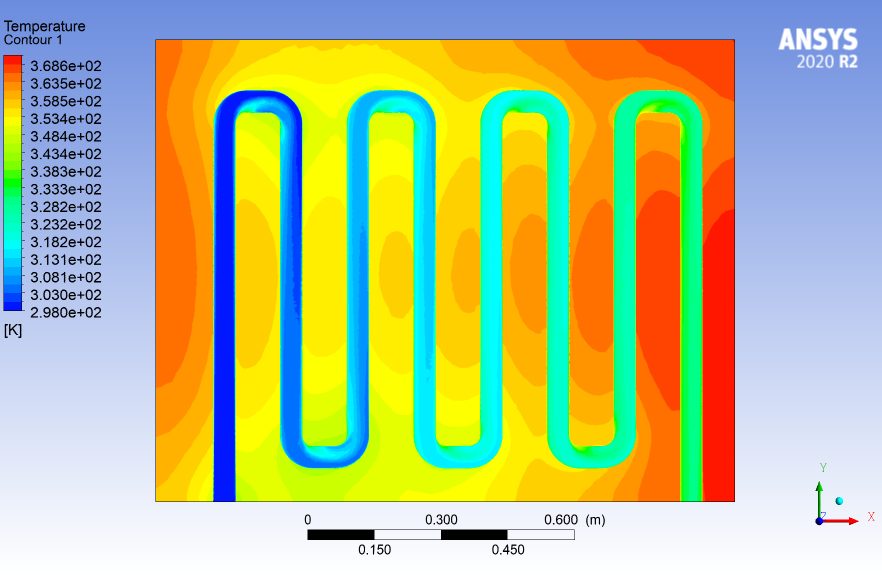
Introduction
Computational Fluid Dynamics (CFD) analysis stands as a formidable tool within the realms of engineering and thermodynamics, where understanding the intricacies of heat transfer and optimizing heat exchangers is of paramount importance. This article explores the critical role of CFD analysis in the context of double pipe heat exchangers. To begin with, CFD, or Computational Fluid Dynamics, is a sophisticated numerical tool that has revolutionized the way engineers analyze and design systems involving fluid flow and heat transfer.
It essentially transforms complex physical phenomena into a digital realm, allowing for detailed, accurate simulations of fluid behavior within a given system. This process is an invaluable asset for engineers and designers, particularly in the realm of heat exchangers, where efficiency, energy conservation, and cost-effectiveness are at the forefront of design considerations.
Working Principle of Double Pipe Heat Exchanger
Before we delve into the significance of CFD analysis, it’s essential to understand the basic operating principles of a double pipe heat exchanger. These exchangers are widely employed for their simplicity, compact design, and effectiveness in transferring heat between two fluids. The heart of a double pipe heat exchanger lies in its arrangement: two concentric pipes of different diameters, with one fluid flowing inside the inner pipe (tube side) and another fluid passing through the annular space formed between the two pipes (shell side).
These two fluids can be hot and cold water, oil, or various other media, depending on the specific application. The heat transfer occurs through the walls of the inner tube, enabling the exchange of thermal energy between the two fluids without them coming into direct contact. What distinguishes different double pipe heat exchangers is the arrangement of the tube and shell sides, typically configured as parallel flow or counterflow. In a parallel flow heat exchanger, both the hot and cold fluids flow in the same direction, entering at one end and exiting at the other. In a counterflow heat exchanger, the fluids flow in opposite directions, which often leads to higher heat transfer efficiency.
CFD Analysis and Its Significance
CFD analysis plays a pivotal role in the design and analysis of double pipe heat exchangers, but why is it so significant? In the realm of heat exchangers, CFD analysis stands as an invaluable tool for several reasons. It allows engineers to virtually recreate the behavior of fluids within the exchanger, providing insights into temperature distribution, flow patterns, pressure drops, and other critical parameters. In a complex heat exchanger, it can be extremely challenging to predict how different design parameters, such as tube diameter, length, or the type of fluid, will affect the overall performance.
This is where CFD analysis shines. By numerically solving the governing equations that describe fluid flow and heat transfer, CFD software can simulate various operating conditions and design alternatives, enabling engineers to make informed decisions based on quantitative data. This process simplifies the task of optimizing heat exchanger designs, troubleshooting issues, and evaluating different configurations, all while avoiding costly and time-consuming physical prototyping.
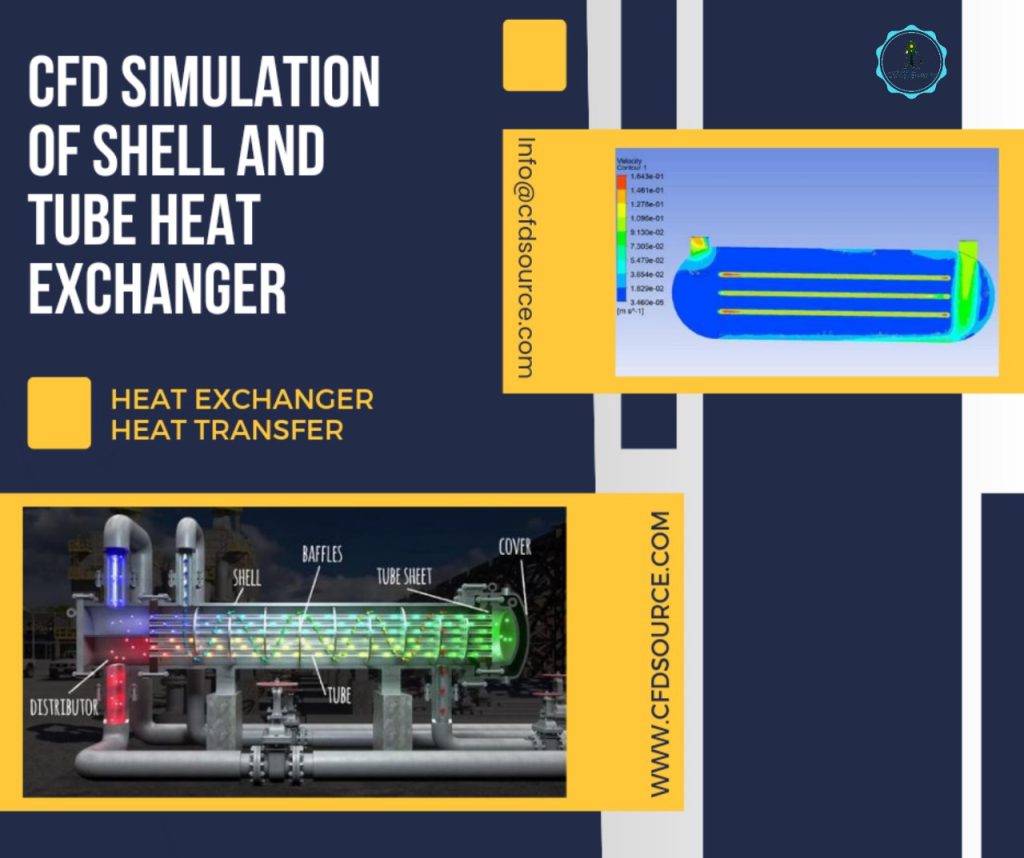
Steps in Conducting a CFD Analysis
To comprehend the role of CFD analysis in heat exchangers, it is essential to break down the process into a series of steps. The first step involves creating a virtual model of the heat exchanger, including its geometry and dimensions. Accurate representation of the geometry is essential because it directly influences the accuracy of the simulation. The next step is meshing, where the entire computational domain is divided into small elements or cells. This mesh represents the space within the heat exchanger and is crucial for numerical simulations. The finer the mesh, the more detailed the simulation, but it also demands more computational resources.
Once the mesh is ready, engineers define boundary conditions. These conditions include specifying parameters such as fluid properties (viscosity, thermal conductivity, etc.), inlet and outlet conditions (flow rates, temperatures), and the material properties of the heat exchanger components. Properly setting these boundary conditions is essential for an accurate simulation that mirrors real-world conditions. With the geometry, mesh, and boundary conditions in place, the CFD software proceeds to solve the governing equations for fluid flow and heat transfer. These equations, including the Navier-Stokes equations and energy conservation equations, describe the behavior of fluids in the exchanger. Solving these equations numerically provides predictions of temperature distribution, pressure drop, and other critical parameters.
Finally, post-processing is conducted to visualize and interpret the results. Engineers use various tools within the CFD software to generate contour plots, streamlines, and velocity vectors, aiding in the understanding of flow behavior and heat transfer characteristics. The entire process allows engineers to make informed decisions, refine designs, and optimize heat exchangers for enhanced performance and efficiency.
Benefits of CFD Analysis in Heat Exchanger Design
The implementation of CFD analysis in heat exchanger design carries several significant benefits. First and foremost, it leads to improved efficiency. By employing CFD, engineers can fine-tune heat exchanger designs to maximize thermal performance. This results in better heat transfer and reduced energy consumption, ensuring that the heat exchanger operates at its optimal capacity. Improved efficiency is not only advantageous in terms of energy conservation but also translates into cost reduction.
Energy-efficient heat exchangers consume less power, leading to substantial operational cost savings over the long term. Furthermore, CFD analysis mitigates the need for costly physical prototypes and extensive trial-and-error testing, making the design process more economical. By identifying and addressing potential issues through simulations, engineers can avoid unnecessary expenses and delays.
Additionally, enhancing energy efficiency has a positive environmental impact. Reduced energy consumption means lower greenhouse gas emissions, contributing to a more sustainable and eco-friendly operation. In essence, CFD analysis equips engineers with the tools to create heat exchangers that are both economically and environmentally responsible, thus ensuring the best of both worlds.
Challenges and Limitations
While CFD analysis is a powerful tool, it is not without its challenges and limitations. One of the primary challenges lies in the computational resources required. Conducting CFD simulations, especially for complex heat exchangers, demands significant processing power and memory. This can be cost-prohibitive for smaller organizations or projects with limited computing infrastructure. Additionally, the computational time for highly detailed simulations can be lengthy, which may not be suitable for time-sensitive applications.
Another challenge is striking a balance between accuracy and speed. Increasing the accuracy of CFD simulations typically requires finer mesh resolutions and longer computational times. While highly detailed simulations can provide more precise results, they might not always be practical for every design phase or operational scenario. Engineers often face the dilemma of choosing a level of detail that aligns with project constraints and goals. It is essential to recognize that the efficacy of CFD analysis relies on skilled professionals who can navigate these challenges and make informed decisions that strike the right balance between computational demands and the desired level of accuracy.
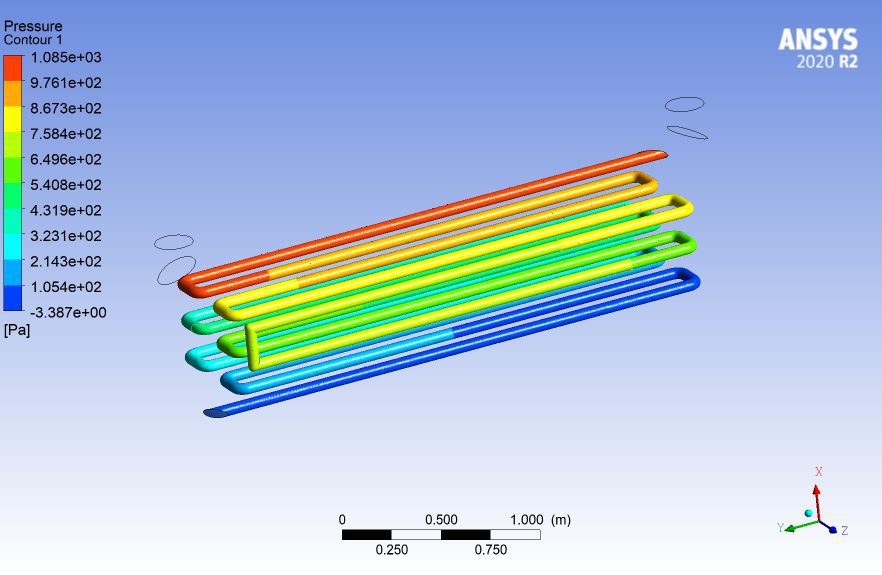
Real-World Applications
The real-world applications of double pipe heat exchangers are diverse, spanning across industries and research domains. In industrial settings, these heat exchangers are commonly used in chemical plants, refineries, and manufacturing facilities. Their primary purpose is to control temperatures during various processes, ensuring that products and equipment remain within specified operational ranges. The HVAC (Heating, Ventilation, and Air Conditioning) sector also extensively employs double pipe heat exchangers to regulate air temperature in buildings.
These systems play a pivotal role in maintaining comfortable indoor environments, particularly in regions with extreme temperature variations. Beyond industrial and HVAC applications, double pipe heat exchangers are integral to research and development. They serve as testbeds for developing new heat transfer technologies, optimizing existing designs, and conducting experiments to further our understanding of thermal systems. Researchers use them to explore innovative ways to enhance heat transfer efficiency and address the challenges of various industries, leading to advancements in the field of heat exchangers as a whole.
Case Study: Optimizing a Double Pipe Heat Exchanger
Let’s examine a real-world case study to illustrate the impact of CFD analysis on optimizing a double pipe heat exchanger’s performance. In XYZ Corporation, a chemical plant faced inefficiencies in its heat exchanger system, resulting in increased energy consumption and operational costs. To address these issues, engineers conducted a comprehensive CFD analysis of the heat exchanger. The analysis allowed them to identify areas of improvement, such as enhancing the heat exchanger’s design, modifying flow rates, and optimizing the choice of materials.
By simulating various scenarios and adjusting the parameters accordingly, the engineers achieved a significant reduction in energy consumption, translating to substantial cost savings. The insights gained from the CFD analysis were invaluable, as they not only resolved the existing issues but also set a precedent for ongoing improvements in the plant’s heat exchanger systems. This case study exemplifies how CFD analysis serves as a transformative tool, enabling engineers to fine-tune and enhance the performance of double pipe heat exchangers, ultimately leading to improved energy efficiency and cost-effectiveness in real-world industrial applications.
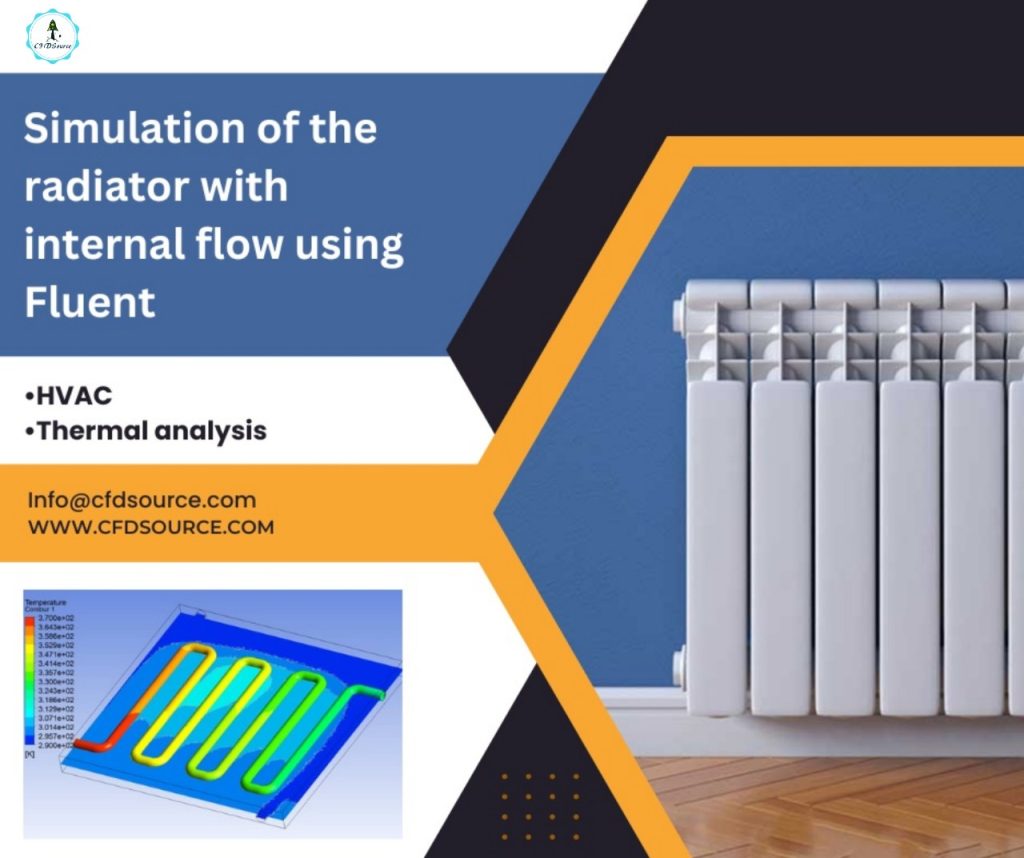
Conclusion
In conclusion, the application of CFD analysis in the context of double pipe heat exchangers represents a groundbreaking approach to heat exchanger design and optimization. The article has highlighted the pivotal role of CFD in achieving superior efficiency, reduced operational costs, and a positive environmental impact. CFD allows engineers to bridge the gap between theoretical design and real-world performance, enabling them to explore a wide range of design variations without the need for physical prototypes. By virtually simulating fluid flow and heat transfer within double pipe heat exchangers, engineers can fine-tune critical parameters, optimize performance, and address potential issues, ultimately leading to heat exchangers that operate at their peak capacity.
CFD analysis of double pipe heat exchanger: This not only contributes to significant cost savings in terms of energy consumption and operational expenses but also aligns with sustainability goals by reducing greenhouse gas emissions. However, it’s important to acknowledge the challenges and limitations of CFD, including the computational resources required and the trade-off between accuracy and simulation speed. Engineers must carefully balance these factors to make the most of CFD analysis in practical applications. With real-world examples and practical insights, it is evident that CFD analysis is a transformative tool for designing and optimizing double pipe heat exchangers, offering a path toward enhanced performance and sustainability in various industrial, HVAC, and research settings.