CFD thermal analysis: Computational Fluid Dynamics (CFD) has emerged as a groundbreaking context in the field of engineering and scientific analysis. It gives a digital laboratory in which complicated fluid dynamics and warmth transfer phenomena may be discovered, analyzed, and optimized. CFD includes the usage of numerical techniques and algorithms to simulate and investigate fluid flow, warmth switch, and their interaction. This generation has opened doorways to a generation in which engineers and scientists can dive deep into the tricky details of fluid conduct, temperature distributions, and lots more. It is a device that has revolutionized numerous industries and research domain names by presenting a deeper understanding of the way fluids circulate and how heat is transferred inside structures. In this article, we can explore one side of CFD, specifically its position in thermal analysis, and highlight the significance of heat switches in this context.
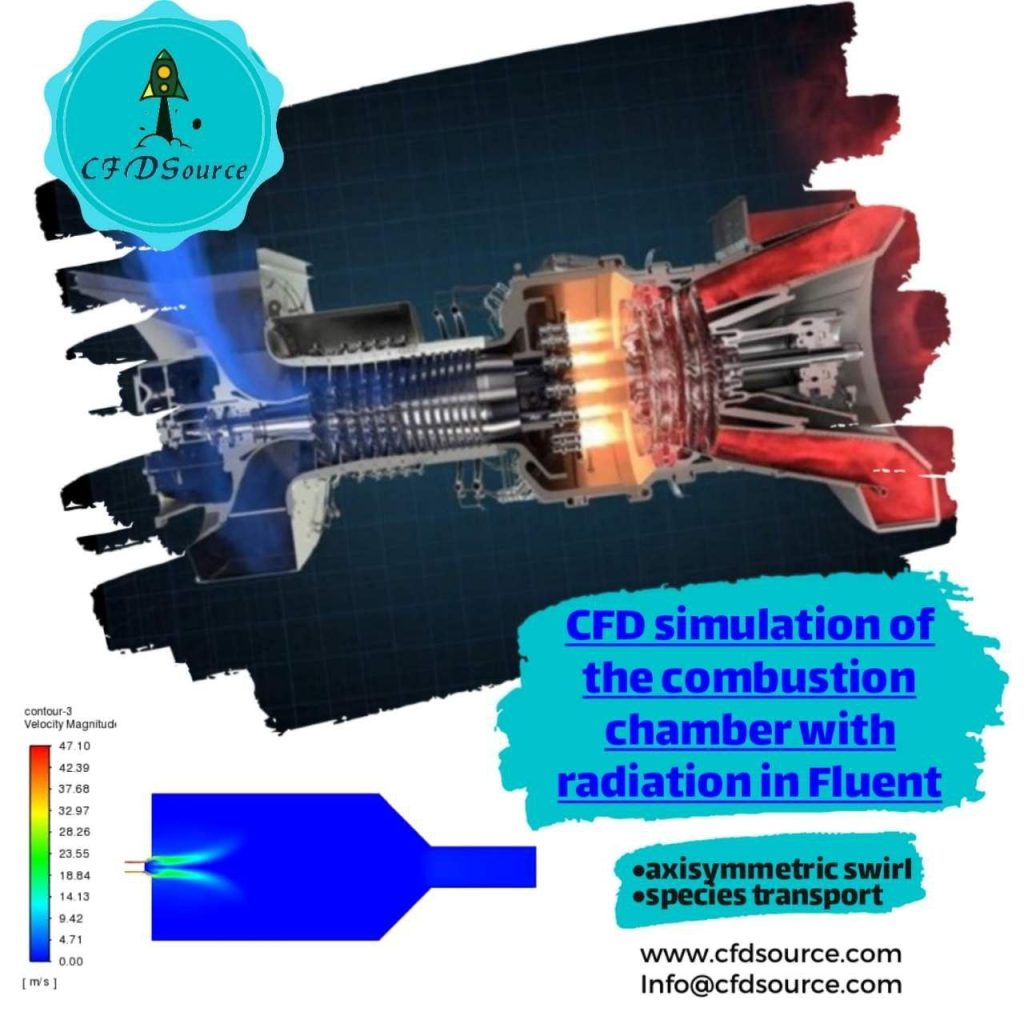
What is CFD?
In the sector of engineering and technology, thermal analysis is a basic aspect that affects the design, performance, and safety of infinite systems. It revolves around knowing of how heat actions within the system, and the way temperature distributions alternate through the years. When it comes to analyzing these heat switch phenomena, CFD takes the leading edge. Computational Fluid Dynamics -based thermal analysis equips engineers with a valuable device to study the distribution and switch of heat through a given process. This includes analyzing how heat power transferred within the points, how temperature slopes evolve, and its effect on the general overall performance of the device. From the cooling of electronic ingredients to the efficiency of energy system, Computational Fluid Dynamic-based thermal analysis is essential for optimizing and to ensure the validity of different systems across industries.
Thermal Analysis with CFD
In the world of engineering and science, thermal analysis is a pivotal component that influences the design, performance, and safety of countless systems. It revolves around understanding how heat moves within these systems, and how temperature distributions change over time. When it comes to studying these heat transfer phenomena, Computational Fluid Dynamics takes the forefront. CFD-based thermal analysis provides engineers with an invaluable tool to study the distribution and transfer of heat within a given system. This involves analyzing how heat energy is transferred from one point to another, how temperature gradients evolve, and what impact this has on the overall performance of the system. From the cooling of electronic components to the efficiency of energy systems, CFD-based thermal analysis is pivotal in optimizing and ensuring the reliability of various systems across different industries.
Importance of Heat Transfer in CFD
The importance of heat transfer in the field of CFD can’t be exaggerated. Heat transfer is at the center of many engineering and scientific procedures, affecting everything from the effectiveness of industrial systems to the consolation of our dwelling areas. Within CFD, the knowledge warmth switch is important because it lets engineers and scientists predict and optimize the conduct of fluids on the subject of temperature variations. The movement of heat inside a system can be equalized to dancing of electricity, influencing the overall performance and stability of components.

For example, in the subject of electronics, powerful cooling is crucial to prevent overheating, which may cause issue failure. In the aerospace, the effective transfer of heat performs an important role in designing and performance of plane engines. Computational Fluid Dynamics permits experts to model these heat transfer procedures, making it viable to excellent-track structures for the best effectiveness and safety. In fact, Computational Fluid Dynamics and heat transfer are inseparable, and their synergy is significant for solving engineering challenges in real world.
Applications of CFD Thermal Analysis
The programs of Computational Fluid Dynamics thermal analysis are as numerous as processes and methods they are investigating. In different industries, Computational Fluid Dynamics thermal analysis performs an essential function in optimization and innovation. In the field of aerospace, it is utilized to increase the design of spacecraft and aircraft, ensuring that they can resist the acute heat generated during the flight. This technology is similarly pivotal in the car industry, where It is used to fine-tune engine cooling processes and enhance gasoline performance. Moreover, Computational Fluid Dynamics thermal analysis is instrumental within the field of energy, where it helps for designing more effective and sustainable energy generation processes.
In the electronics sector, Computational Fluid Dynamics facilitates saving you from overheating in digital devices to ensure the reliability and performance. Additionally, the development enterprise makes use of Computational Fluid Dynamics to optimize HVAC (heating, ventilation, and air condition) processes for electricity efficiency and occupant comfort. The extensive spectrum of programs underscores the flexibility of Computational Fluid Dynamics thermal analysis to address challenges of the real world.
The Role of Simulations
Simulation is in the center of Computational Fluid Dynamics thermal analysis, has a vital position in knowing and anticipating how heat is transferred within processes. Through the power of simulation, scientists and engineers create digital displays of real word processes, breaking them into infinitely smaller components. These components interact with each other to imitate the behavior of fluids flow and heat transfers.
Simulation is in the center of Computational Fluid Dynamics thermal analysis, has a vital position in knowing and anticipating how heat is transferred within processes. Through the power of simulation, scientists and engineers create digital displays of real word processes, breaking them into infinitely smaller components. These components interact with each other to imitate the behavior of fluids flow and heat transfers.
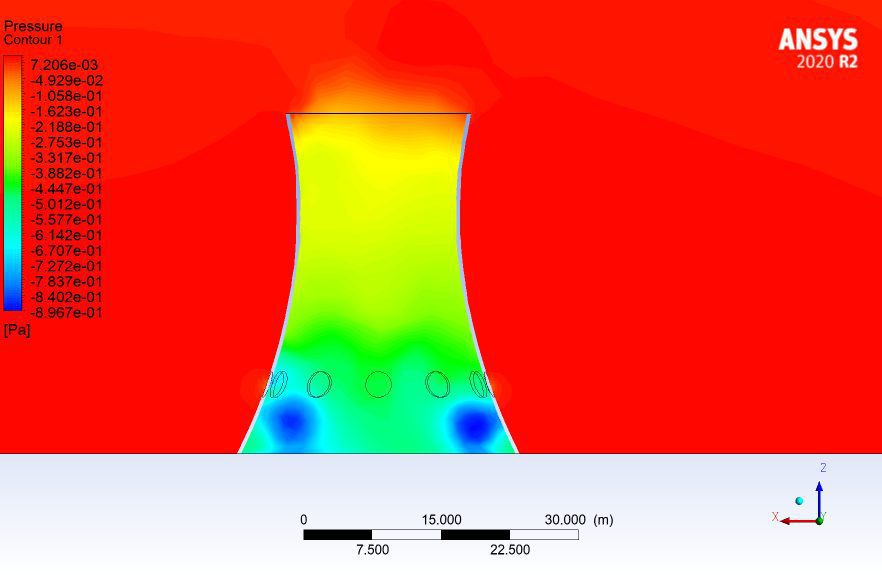
CFD Software and Tools
To conduct Computational Fluid Dynamics thermal analysis, engineers depend on specialized software programs and equipment that have been engaged to deal with the complicated arithmetic and computational factors concerned within the system. These software programs offer a consumer-friendly interface for setting up simulations, define boundary situations, and visualize the outputs. Industry-standard Computational Fluid Dynamics software programs, such as COMSOL Multiphysics, ANSYS Fluent, and Open FOAM, provide a broad range of features and abilities for fixing different heat transfer challenges.
This equipment provides pre-configured fashions and templates for special applications and enable engineers to expedite analyses. Moreover, they comprise libraries of predefined substances, boundary situations, and making it less complicated to simulate various situations. The software also offers post-processing abilities, permitting engineers to visualize and interpret simulation consequences, making it simpler to derive visions and optimize device designs. These Computational Fluid Dynamics software applications have become indispensable sources that help engineers to work on thermal analysis.
Steps in Conducting CFD Thermal Analysis
The manner of conducting Computational Fluid Dynamics thermal analysis is a well-described and systematic package of steps. It includes numerous crucial steps that collectively cause comprehensive knowing of heat transfer within a system. The first step is to describe the problem. Engineers should set up the objectives of the evaluation and determine the parameters to be investigated. Then, developing a mesh is critical. The mesh is a grid that divides the domain into small parts for simulation. The grid has to be refined in regions in which heat transfer is predicted to be important. Setting up boundary situations is the next vital step, pressure, specific temperature, and different parameters in the process’s boundaries.
Once it is defined, solving some equations—usually the heat equation for temperature and Navier-Stokes equations for fluid flow—is done numerically with the use of the Computational Fluid Dynamics software. This computation provides output on fluid flow styles and temperature distributions. The last step includes post-processing, where engineers imagines and interpret the outputs. They investigate the simulation information to make right choices about machine design and overall performance optimization. The reliability and accuracy of Computational Fluid Dynamics thermal analysis mostly depend on the high quality and precision of each steps, underscoring the significance of a systematic insight.
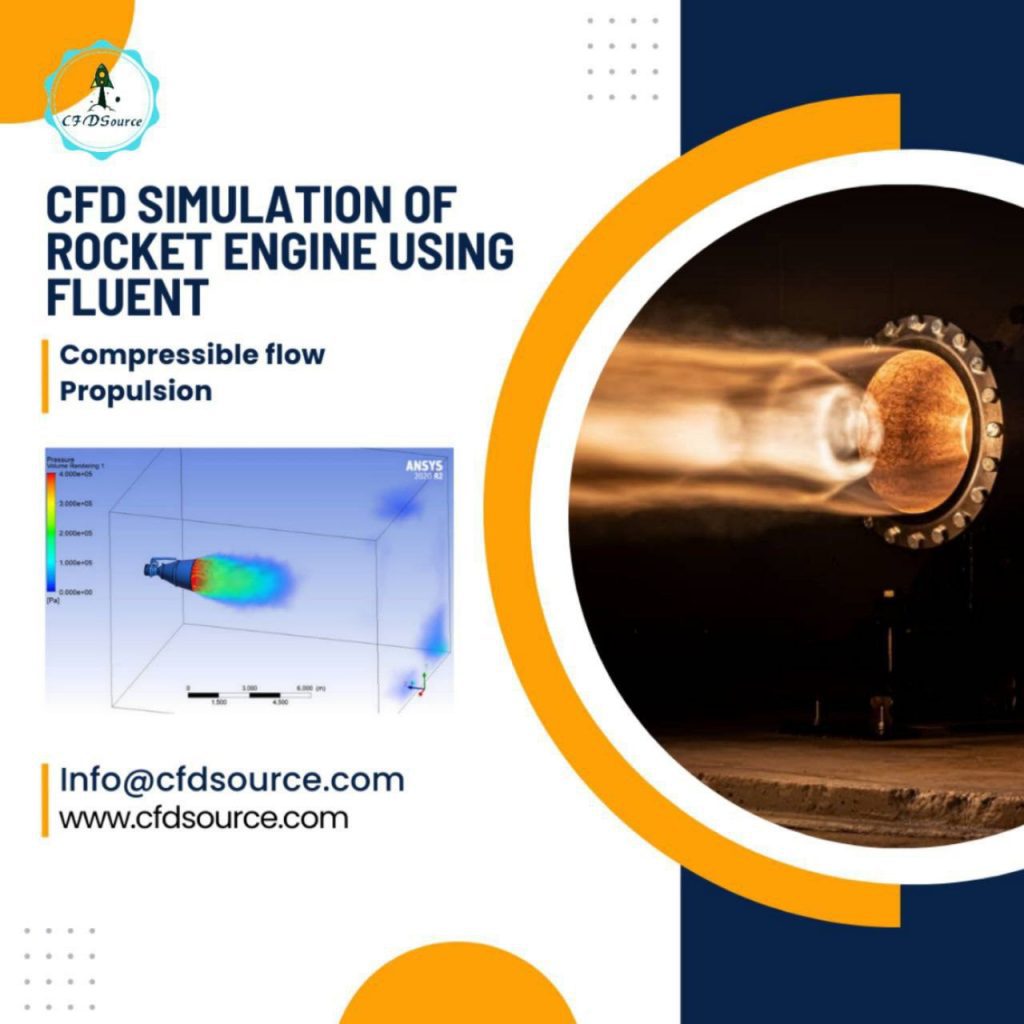
Challenges in CFD Thermal Analysis
While CFD thermal analysis gives a powerful device to know heat transfer and fluid flow, it isn’t without its problems. In this field, researchers facing to several obstacles that require modern solutions. One of the common problems is meshing, a method to create a grid that divides the area into smaller cells for simulation. To Achieve a suitable mesh that display accurate system’s geometry even as it is computationally effective, can be a sensitive stability. Solver convergence is other problem. It refers to the potential of the numerical algorithms to attain an accurate and stable solution.
Convergence issues can occur due to complicated float behavior or incorrect boundary situations. Choosing an appropriate turbulence model for simulations is but another hurdle. Different flows show diverse turbulence characteristics, and choosing the right model to capture those functions correctly is an important selection. Furthermore, validation of Computational Fluid Dynamics consequences towards experimental information is often tough, as experiments themselves can also have limitations and uncertainties. Despite those challenges, the non-stop advancements in Computational Fluid Dynamics generation, coupled with the understanding of engineers and scientists, allow for the improvement of innovative answers to address those issues.
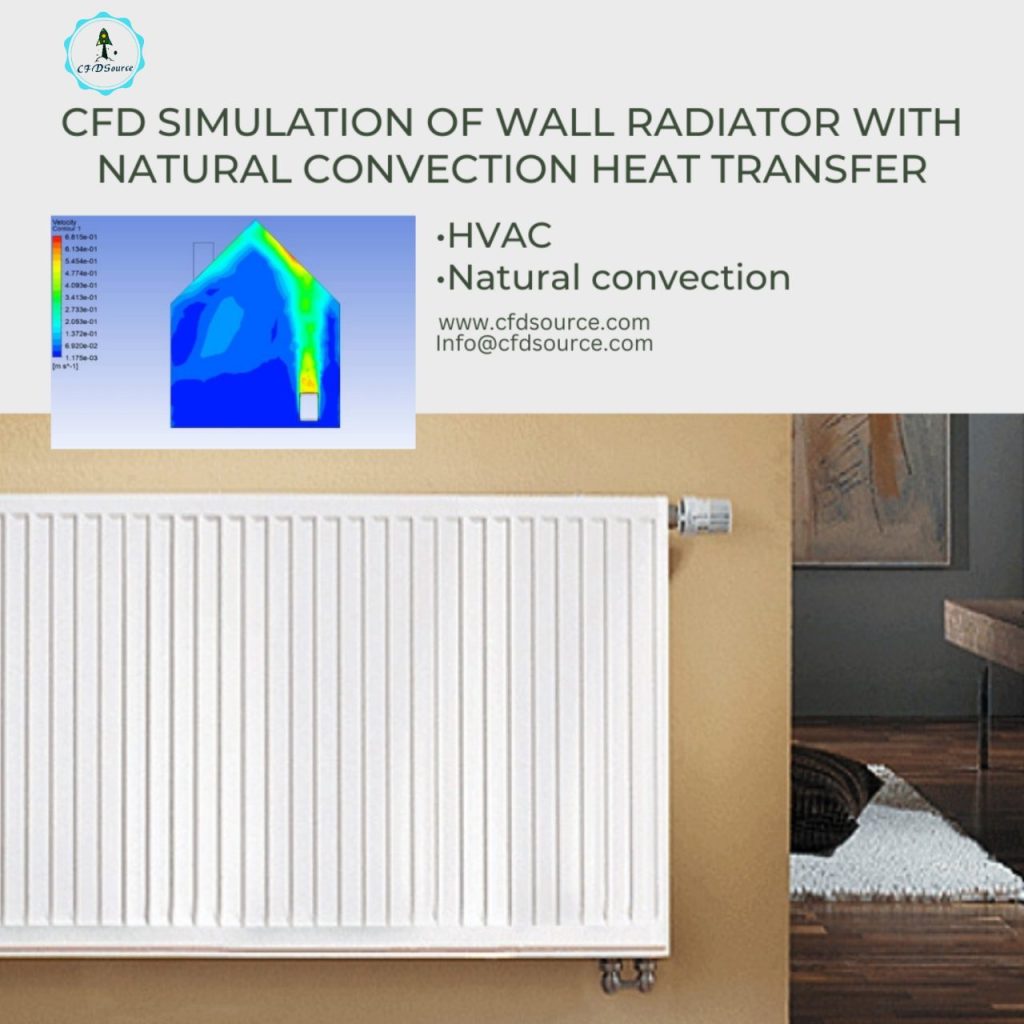
Advancements in Heat Transfer CFD
The field of heat transfer Computational Fluid Dynamics has witnessed important improvements in recent years, permitting researchers to conduct correct simulations and acquire right approaches into thermal phenomena. One of the significant progress is the improvement of excessive-constancy models for turbulence. These models boost the anticipate of turbulence features, permitting more accurate simulations of heat transfer. Moreover, the combining of learning machine and artificial intelligence in Computational Fluid Dynamics software programs has simplified the system of model setting up, meshing, and post-processing and to make it more efficient.
Further, improvements in computing strength have allowed for the simulation of larger and more complicated structures, offering a more knowable of heat transfer systems. The aggregate of those progresses has improved the accuracy of simulations and additionally decreased the time that required for analysis, making Computational Fluid Dynamics thermal analysis a more practical and available tool for engineers. As the technology keeps evolving, we can anticipate similar breakthroughs to increase the skills of heat transfer Computational Fluid Dynamics (CFD).
Real-World Examples
The practicality and significance of Computational Fluid Dynamics (CFD) thermal analysis come to be obvious analyzing application of real-world examples. In the car industry, engineers use Computational Fluid Dynamics simulations to optimize engine cooling processes. By evaluating the flow of heat and air transfer inside the engine compartment, they can design more effective cooling structures, to ensure that engines function at the right temperature and increase fuel efficiency. In the field of electronics, Computational Fluid Dynamics is instrumental to prevent overheating of electronic parts. Engineers figure the flow of air and the distribution of heat within electronic devices, allowing them to design effective cooling solutions and protect the longevity and reliability of sensitive ingredients.
The construction industry leverages Computational Fluid Dynamics for the design of heat-ventilating -air conditioning (HVAC) structures in buildings. Engineers can anticipate temperature distributions and optimize the airflow and heating systems ensuring occupant consolation and energy effectiveness. In the field of aerospace, Computational Fluid Dynamics is essential for optimizing plane design, mainly with the simulation of airflow through engines and over wings. This guarantees plane can face up to high-temperature conditions and hold aerodynamic performance. The real-world examples underscore the valuable position of Computational Fluid Dynamics thermal analysis in several industries, increasing efficiency, safety and performance.
Benefits of CFD Thermal Analysis
CFD has a wide range of benefits in thermal analysis. First and essential, Computational Fluid Dynamics allows researchers and engineers making right design decisions. By simulating heat transfer and fluid flow with the flow within structures, they could anticipate how modifications to a devise’s parts or parameters will affect its performance. This capability to check more than one scenario digitally affects advanced product designs, decreased improvement expenses, and faster time-to-market. Physical prototypes, which are time-consuming and costly to create, can be minimized, if not totally removed.
This accelerate design process and also decrease the financial burdens on companies. Moreover, Computational Fluid Dynamics contributes to improving device efficiency. By knowing how the heat transfer occurs, engineers can optimize designs ensuring that energy is used more successfully, and those components remain within a safe temperature limitation. This is especially crucial for industries consisting of energy and electronics, where efficient cooling and heat controlling can substantially impact overall reliability and performance. To sum up, the benefits of Computational Fluid Dynamics thermal analysis expand from improving design and financial savings to improve system overall performance and competitiveness.
Conclusion
CFD thermal analysis: In conclusion, Computational Fluid Dynamics (CFD) thermal analysis, with its strong emphasis on understanding heat transfer, has become an indispensable tool for engineers and scientists in various industries. Its applications range from optimizing aircraft engines to enhancing the efficiency of HVAC systems in buildings. CFD empowers professionals to simulate and predict complex fluid flow and temperature distributions, leading to improved designs and cost-effective solutions. While challenges like meshing and solver convergence exist, advancements in technology continue to address these hurdles, making CFD even more accurate and accessible. The future holds exciting possibilities, with the integration of AI, real-time simulations, and more user-friendly software. CFD is, without a doubt, a key player in shaping the future of engineering and scientific analysis, promising innovative and sustainable solutions to real-world problems.