The world of engineering is constantly evolving, and one area that has seen significant advancements is the design of turbomachinery through Computational Fluid Dynamics (CFD). In this essay, we will delve into the intricacies of CFD turbomachinery, exploring its applications, advantages, challenges, and the transformative impact it has on the field.
1. Introduction
In the dynamic realm of engineering, where efficiency and precision are paramount, the concept of Computational Fluid Dynamics (CFD) in the context of turbomachinery emerges as a game-changer. Turbomachinery, serving as the beating heart in numerous industries, encompasses a range of devices like turbines and compressors that manipulate fluid flow for various applications. The significance of these components in energy production, aerospace, and manufacturing cannot be overstated.
Traditionally, designing turbomachinery has been a complex task due to the intricate interplay of fluid dynamics. Enter CFD, a revolutionary approach that utilizes numerical methods and simulations to unravel the complexities of fluid behavior. This article embarks on a journey through the intricate landscape of CFD turbomachinery, exploring its applications, challenges, and the transformative impact it brings to the forefront of engineering innovation.
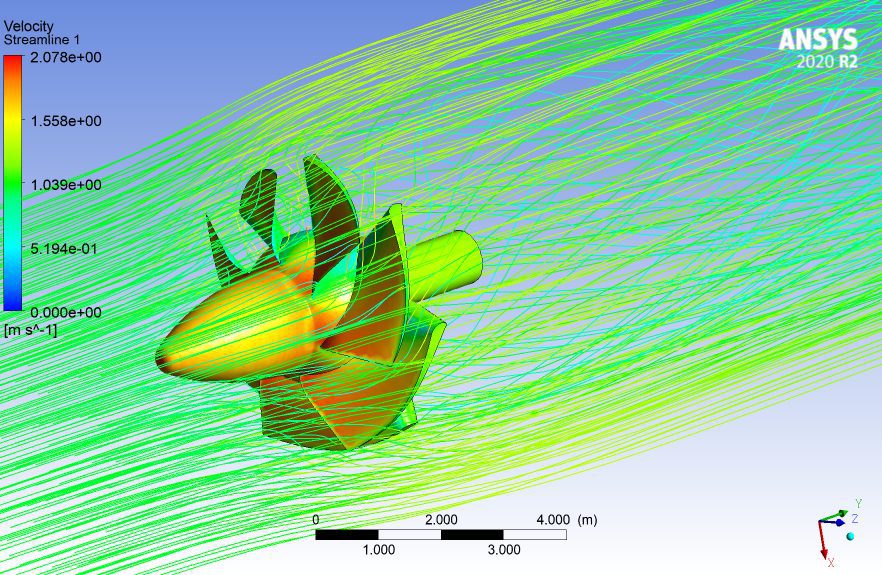
2. Understanding Computational Fluid Dynamics (CFD)
Computational Fluid Dynamics, abbreviated as CFD, is a powerful tool that engineers deploy to comprehend and optimize fluid flow dynamics in turbomachinery design. It involves the use of mathematical models and numerical analysis to simulate the behavior of fluids, enabling a detailed understanding of how they interact with various surfaces and structures. In the context of turbomachinery, where the efficiency of energy conversion is critical, CFD becomes indispensable.
This section will delve into the intricacies of CFD, demystifying its applications and shedding light on how it has become a cornerstone in the design and optimization of turbomachinery components. From simulating airflow over turbine blades to predicting pressure differentials, CFD empowers engineers to make informed decisions that lead to enhanced performance and efficiency.
3. Role of Turbomachinery in Various Industries
Before delving into the specifics of CFD’s role in turbomachinery, it’s crucial to recognize the broad impact turbomachinery has across diverse industries. Turbomachinery serves as a linchpin in sectors ranging from power generation to aviation and beyond. In energy production, turbines play a pivotal role in converting various energy sources into electrical power, while in aviation, jet engines rely on sophisticated compressors and turbines to propel aircraft. Additionally, turbomachinery finds applications in manufacturing processes, where precision and efficiency are paramount. This section explores the multifaceted significance of turbomachinery, setting the stage for understanding how CFD revolutionizes its design and optimization.
4. Challenges in Traditional Turbomachinery Design
Traditionally, designing efficient turbomachinery has been a formidable challenge for engineers. The complexities lie in predicting and understanding fluid dynamics accurately, especially in scenarios where the flow is highly turbulent or involves intricate geometries. Traditional design methods often fall short in providing a comprehensive understanding of how fluids behave within turbomachinery components.
This section will unravel the challenges that engineers face in traditional turbomachinery design, ranging from difficulties in predicting pressure distributions to the limitations of physical prototypes. These challenges paved the way for the adoption of CFD, a cutting-edge approach that mitigates the shortcomings of traditional methods and empowers engineers to achieve unparalleled precision in turbomachinery design.
5. Advantages of Utilizing CFD in Turbomachinery Design
The integration of Computational Fluid Dynamics (CFD) into the realm of turbomachinery design heralds a multitude of advantages that have transformative implications for the engineering landscape. One of the paramount benefits lies in the ability of CFD to overcome the limitations of traditional design methods. Unlike physical prototypes that may be constrained by time and resources, CFD simulations provide engineers with a virtual testing ground to explore various design configurations, iterate rapidly, and optimize performance.
Additionally, CFD enables a detailed understanding of fluid behavior within turbomachinery components, allowing for precise adjustments to enhance efficiency and minimize energy losses. The cost-effectiveness of CFD in comparison to traditional testing methods further contributes to its appeal, as it allows for comprehensive design exploration without the need for extensive physical prototypes. In essence, the advantages of CFD in turbomachinery design extend beyond efficiency gains, encompassing cost savings and unprecedented flexibility in the pursuit of optimal design solutions.
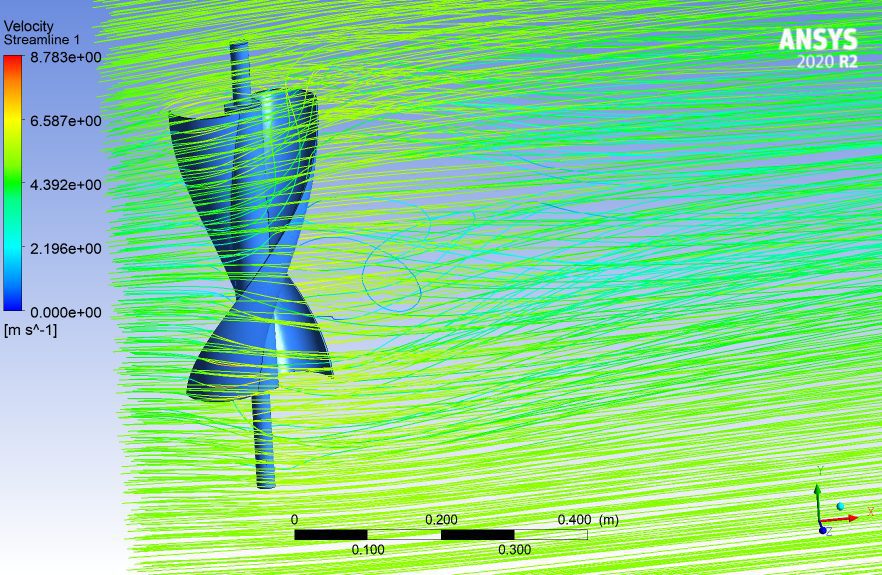
6. Key Components of CFD Turbomachinery Analysis
To harness the full potential of Computational Fluid Dynamics (CFD) in turbomachinery design, engineers must navigate a landscape of key components integral to the analysis process. Firstly, defining accurate boundary conditions is paramount. These conditions dictate how fluids interact with the surfaces of turbomachinery components and play a pivotal role in obtaining realistic simulations. Mesh generation, the process of discretizing the geometry into smaller elements, is another crucial component.
The quality and refinement of the mesh significantly impact the accuracy of CFD results. Selecting appropriate turbulence models, which describe the turbulent behavior of fluids, is equally vital. Solver settings, post-processing techniques, and validation against experimental data round out the essential components of CFD turbomachinery analysis. This section will delve into each of these components, unraveling their significance and providing insights into the intricacies of conducting a comprehensive CFD analysis for turbomachinery design.
7. Simulation Software for CFD in Turbomachinery
The efficacy of Computational Fluid Dynamics (CFD) in turbomachinery design is closely tied to the capabilities of simulation software. A myriad of tools exists, each offering unique features tailored to the specific needs of turbomachinery analysis. This section will provide an overview of popular simulation software, such as ANSYS, COMSOL, and OpenFOAM, highlighting their strengths and applications in the context of turbomachinery design. These tools encompass a range of functionalities, including mesh generation, solver algorithms, and post-processing capabilities.
The choice of simulation software depends on factors such as the complexity of the analysis, the size of the turbomachinery components, and the specific requirements of the engineering project. By understanding the capabilities of different simulation software options, engineers can make informed decisions, selecting the tool that aligns with the objectives of their turbomachinery design endeavors.
8. Real-world Applications of CFD in Turbomachinery Design
The true litmus test of any technology lies in its real-world applications, and Computational Fluid Dynamics (CFD) in turbomachinery design stands out as a proven and impactful tool. This section will delve into diverse examples across industries, showcasing instances where CFD simulations have not only addressed challenges but also led to groundbreaking advancements.
From optimizing the aerodynamics of aircraft engines to enhancing the efficiency of industrial compressors, CFD has left an indelible mark on turbomachinery design. Case studies will be explored, illustrating how CFD has enabled engineers to fine-tune designs, reduce development costs, and accelerate the time-to-market for turbomachinery components. By examining these real-world applications, a compelling narrative emerges, highlighting the tangible benefits that CFD brings to the forefront of turbomachinery engineering.
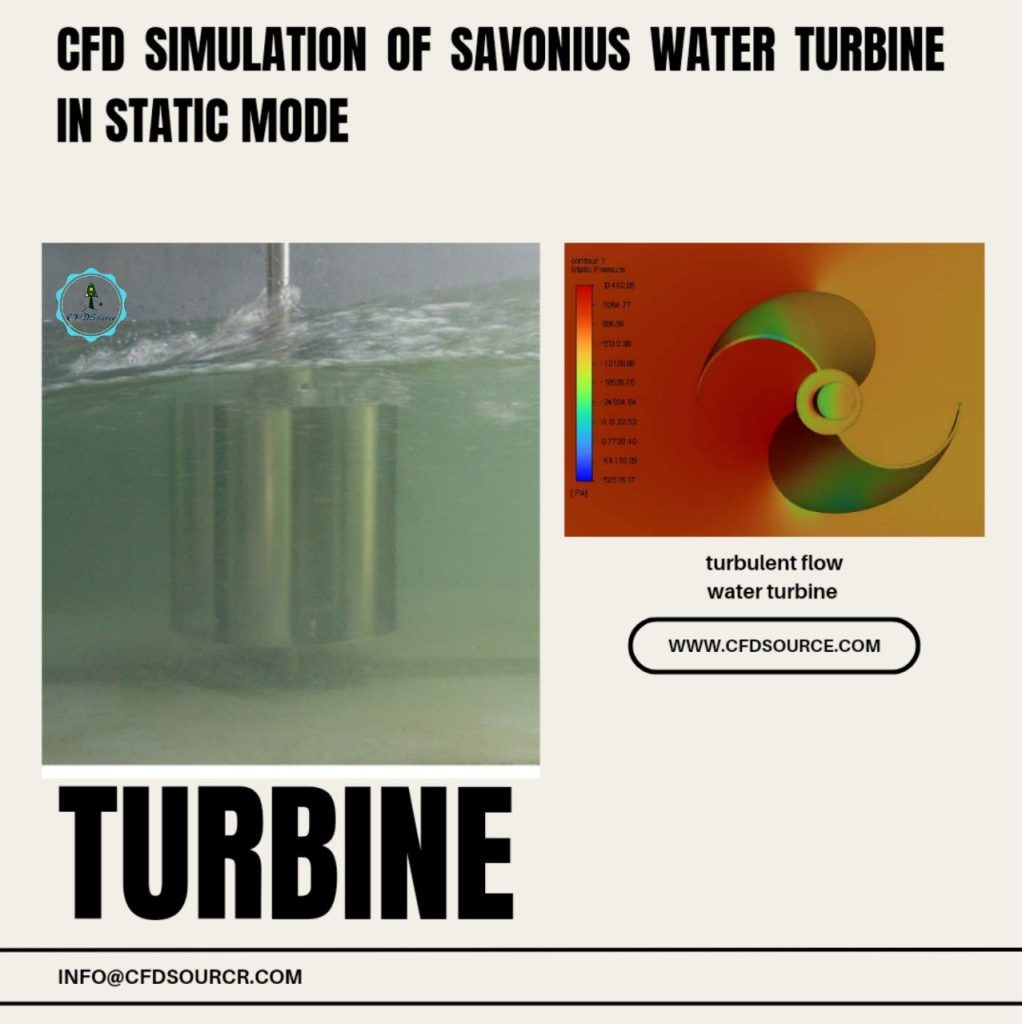
9. Improving Efficiency and Performance
The overarching goal in turbomachinery design is to achieve optimal efficiency and performance, and Computational Fluid Dynamics (CFD) emerges as an instrumental tool in this pursuit. By simulating fluid flow within turbomachinery components, engineers gain valuable insights into the intricate dynamics at play. This section will delve into how CFD facilitates the iterative optimization of designs, enabling engineers to fine-tune parameters such as blade profiles, inlet geometries, and operating conditions.
The ability to predict and mitigate issues such as flow separation, turbulence, and pressure losses is paramount in enhancing the overall efficiency of turbomachinery. Through the lens of CFD, engineers can explore a myriad of design possibilities, identifying configurations that maximize energy conversion and minimize wasteful losses. The result is a paradigm shift in turbomachinery design, where efficiency and performance are not only objectives but tangible outcomes of a systematic and informed approach facilitated by CFD simulations.
10. Challenges in Implementing CFD in Turbomachinery Design
While Computational Fluid Dynamics (CFD) presents a plethora of advantages, its implementation in turbomachinery design is not without its challenges. This section will navigate through the hurdles engineers may encounter, ranging from the computational demands of complex simulations to the intricacies of handling geometric complexities. High-fidelity simulations, crucial for accurate results, often require substantial computational resources, leading to extended simulation times and increased costs.
Moreover, the diverse geometries inherent in turbomachinery components pose challenges in creating meshes that accurately represent the intricate surfaces. Specialized expertise in CFD is essential, adding another layer of complexity for engineering teams. However, the payoff in terms of design precision, efficiency gains, and reduced physical testing can far outweigh these challenges. By acknowledging and addressing these hurdles head-on, engineers can maximize the benefits of CFD in turbomachinery design and propel the field into new frontiers of innovation.
11. Recent Innovations and Trends in CFD Turbomachinery
The landscape of Computational Fluid Dynamics (CFD) in turbomachinery design is dynamic, with continuous innovations and evolving trends shaping the trajectory of the field. This section will delve into recent advancements, exploring how machine learning integration, cloud-based simulations, and other cutting-edge technologies are reshaping the way engineers approach turbomachinery design. Machine learning algorithms are increasingly being employed to enhance the accuracy and speed of CFD simulations, offering a more nuanced understanding of fluid behavior.
Cloud-based simulations, on the other hand, provide scalable and cost-effective solutions, allowing engineers to conduct simulations without the need for extensive local computing resources. By staying abreast of these innovations and trends, engineers can position themselves at the forefront of turbomachinery design, harnessing the latest technologies to push the boundaries of what is possible in the realm of CFD.
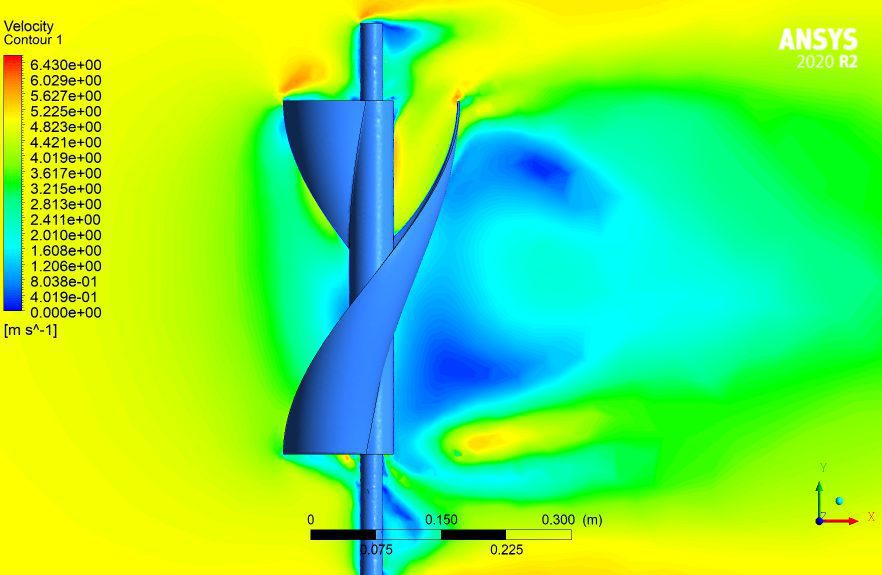
12. Case Studies
Examining specific case studies serves as a window into the tangible impact and success of Computational Fluid Dynamics (CFD) in turbomachinery design. This section will dissect noteworthy examples where CFD simulations have played a pivotal role in overcoming design challenges and achieving remarkable results. From optimizing the efficiency of a gas turbine in a power plant to refining the aerodynamics of a propeller in marine applications, case studies showcase the versatility of CFD across diverse industries.
By delving into the details of each case, we can unravel the nuances of the challenges faced, the methodologies employed, and the outcomes achieved through CFD-driven design enhancements. These real-world applications not only underscore the efficacy of CFD but also provide valuable insights and best practices for engineers looking to leverage this powerful tool in their turbomachinery design endeavors.
13. Future Prospects and Evolving Technologies
The landscape of turbomachinery design, augmented by Computational Fluid Dynamics (CFD), is poised for continued evolution and innovation. This section will explore the future prospects of CFD in turbomachinery, delving into emerging technologies that are likely to shape the trajectory of the field. As artificial intelligence gains prominence, its integration with CFD promises to revolutionize simulations, offering unprecedented accuracy and efficiency.
Exploring new materials and manufacturing techniques, coupled with advancements in 3D printing, opens avenues for creating turbomachinery components with enhanced performance characteristics. Additionally, the democratization of CFD tools and simulations through user-friendly interfaces and cloud-based platforms is likely to empower a broader range of engineers to harness the benefits of CFD in their designs. By staying attuned to these evolving technologies, engineers can position themselves at the forefront of turbomachinery innovation, driving the field towards a future defined by efficiency, precision, and sustainability.
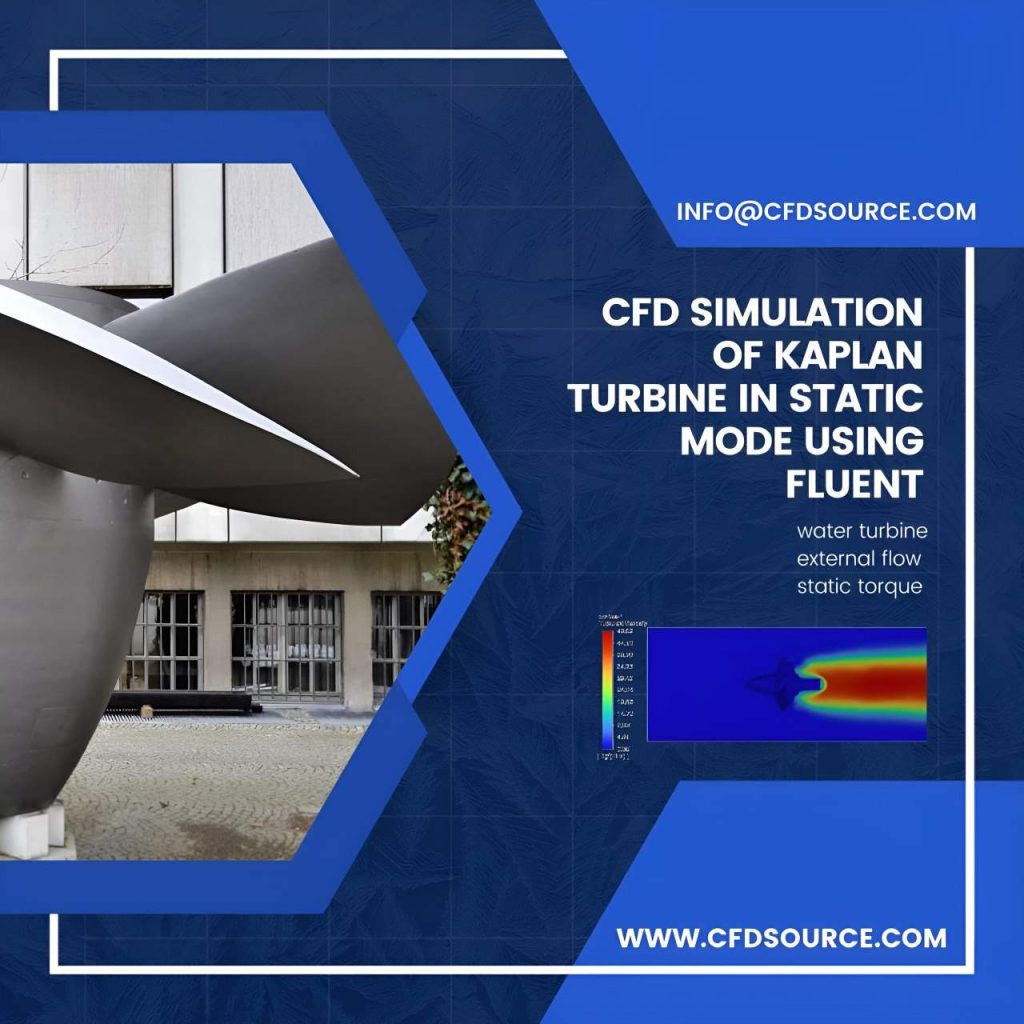
14. Tips for Effective CFD Turbomachinery Simulations
Successfully navigating the realm of Computational Fluid Dynamics (CFD) in turbomachinery design requires a nuanced understanding of effective simulation practices. This section will provide practical tips for engineers embarking on CFD-driven design projects. Firstly, the importance of mesh refinement cannot be overstated. A high-quality mesh, tailored to the specific geometry of turbomachinery components, forms the foundation for accurate simulations.
Validating CFD results against experimental data ensures that simulations align with real-world performance. The significance of post-processing techniques in extracting meaningful insights from simulation results will also be explored. Furthermore, this section will touch upon the iterative nature of CFD simulations, emphasizing the value of exploring multiple design configurations to arrive at optimal solutions. By adopting these tips, engineers can navigate the complexities of CFD turbomachinery simulations effectively, unlocking the full potential of this transformative technology.
15. Conclusion
CFD turbomachinery: In conclusion, the integration of Computational Fluid Dynamics (CFD) has ushered in a new era in turbomachinery design, transcending traditional limitations and opening doors to unprecedented possibilities. This section will summarize the key takeaways, emphasizing how CFD has become an indispensable tool for engineers seeking to optimize efficiency, enhance performance, and overcome design challenges in turbomachinery.
The marriage of CFD and turbomachinery design represents a paradigm shift, where the iterative and data-driven approach afforded by CFD simulations transforms what was once a laborious and resource-intensive process. As we reflect on the transformative impact of CFD in turbomachinery design, it becomes evident that the synergy between cutting-edge simulation technologies and engineering expertise is propelling the field into a future where precision, innovation, and sustainability converge to shape the next generation of turbomachinery components and systems.