What is Y Plus (y+)? Y Plus, also known as y+, is a dimensionless parameter used in fluid mechanics to characterize the behavior of fluid flow near a solid surface. It plays a crucial role in understanding and analyzing boundary layer flows, especially in the context of turbulent flows. In this article, we will delve into the concept of Y Plus, its significance, calculation, and practical applications.
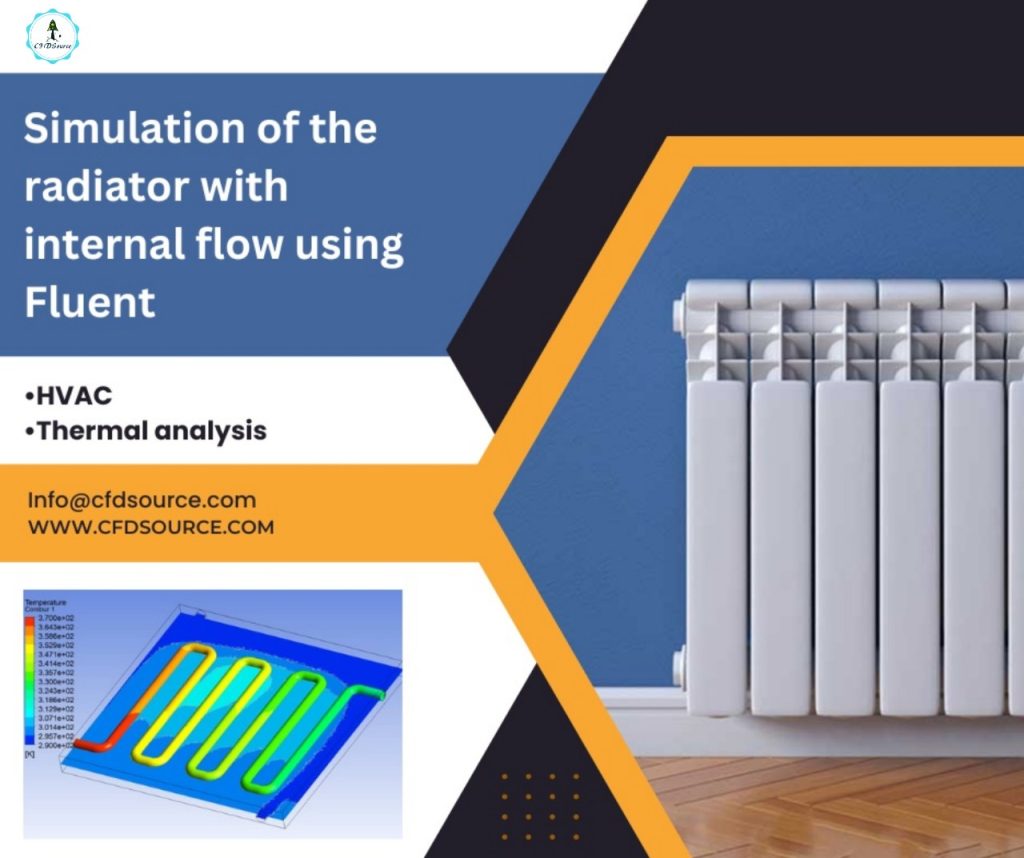
Understanding Y Plus
Understanding Y Plus is essential for grasping the nuances of fluid mechanics, particularly in the context of boundary layer flows. Y Plus, often denoted as y+, is a dimensionless parameter that holds the key to comprehending the flow behavior close to a solid surface. In simple terms, it quantifies how near the flow is to the boundary, shedding light on whether the flow is laminar or turbulent. The Y Plus value is calculated as the ratio of the distance from the wall (y) to the viscous length scale (δ), with δ typically representing the molecular viscosity of the fluid. This ratio is a fundamental aspect of fluid dynamics and serves as a foundation for various applications in industries such as aerospace, automotive, and civil engineering.
Importance of Y Plus in Fluid Mechanics
Y Plus assumes a position of paramount importance in the realm of fluid mechanics due to its significant role in characterizing boundary layer flows. The boundary layer is a thin layer of fluid adjacent to a solid boundary, where the velocity of the fluid transitions from zero at the wall to a maximum value at a certain distance from the wall. Y Plus allows engineers and scientists to decipher the nature of this boundary layer, offering insights into whether the flow is laminar or turbulent.
This distinction is vital because it has far-reaching implications across industries. For instance, in aerospace, understanding Y Plus aids in designing efficient airfoils and wings, while in the automotive sector, it plays a pivotal role in reducing drag and enhancing fuel efficiency. In civil engineering, Y Plus is leveraged to create buildings with shapes that minimize wind-induced forces. Therefore, Y Plus serves as a linchpin in optimizing designs and achieving superior performance in a multitude of practical applications.
Boundary Layer Flow
In the intricate world of fluid mechanics, boundary layer flow stands as a pivotal concept that is closely tied to the understanding of Y Plus. A boundary layer is a thin layer of fluid that directly interacts with a solid surface. Within this layer, the fluid velocity varies from zero at the wall to a maximum value at a certain distance away from the surface. Understanding this layer is critical as it has a profound impact on the behavior of fluids in close proximity to solid boundaries, which is where Y Plus comes into play.
The boundary layer concept is essential in explaining the concept of Y Plus. It is the thin region where the fluid’s viscosity and the solid surface’s effects become significant. The boundary layer can be categorized into two primary types: laminar and turbulent. In laminar boundary layers, the flow is smooth and predictable, with fluid particles moving in parallel layers. In contrast, turbulent boundary layers are characterized by chaotic and unpredictable fluid motion.
Boundary layers have a critical role in various applications, from aerodynamics and hydrodynamics to heat transfer and chemical engineering. For instance, in aerodynamics, the understanding of boundary layers helps in designing aircraft wings and airfoils. By manipulating the boundary layer, engineers can optimize lift and reduce drag, which are crucial factors in aircraft performance. Moreover, in the study of heat transfer, boundary layers affect how efficiently heat is transferred from a solid surface to the surrounding fluid. A comprehension of boundary layers is, therefore, essential for the development of effective heat exchangers and cooling systems.
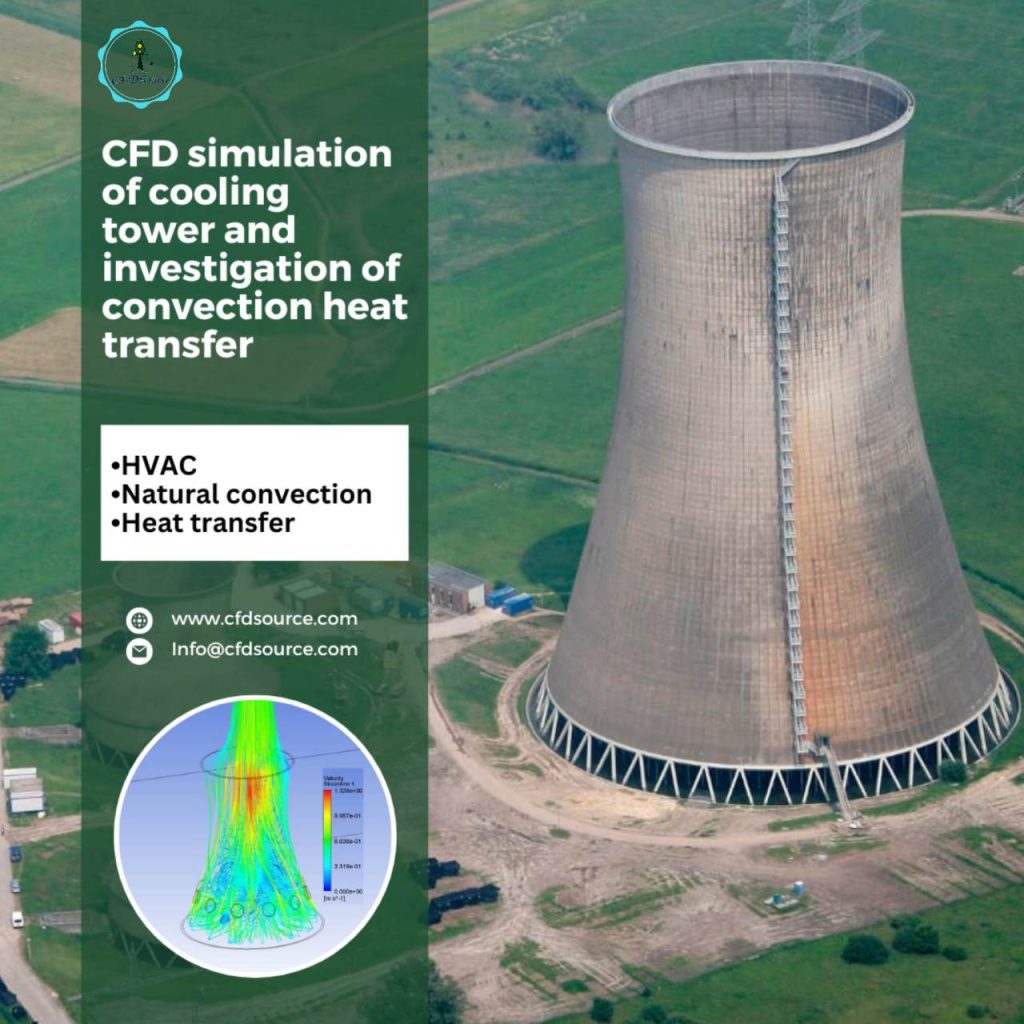
Significance of Y Plus in Turbulent Flow
Turbulent flow is a complex and chaotic form of fluid motion, characterized by irregular, eddying currents. In turbulent flows, the concept of Y Plus plays a crucial role, primarily in defining the transition between the viscous sub-layer and the outer layer. The viscous sub-layer is the region of the boundary layer closest to the solid surface where the flow is strongly influenced by viscosity. The outer layer, on the other hand, is the region further from the surface where the flow is less influenced by viscosity and behaves more chaotically.
Understanding this transition is of paramount importance in turbulent flows. Y Plus helps pinpoint the point at which the flow transitions from the viscous sub-layer to the outer layer. This transition has a significant impact on various fluid dynamic phenomena. For instance, in fluid drag analysis, it determines the boundary between skin friction drag (caused by the viscous sub-layer) and pressure drag (caused by the outer layer). By accurately determining this transition point, engineers can make precise predictions about the drag forces acting on an object in turbulent flow, which is vital in fields like automotive design and aerodynamics.
Moreover, the behavior of Y Plus in turbulent flows provides valuable insights into the distribution of velocity and other fluid properties near a solid surface. These insights are crucial in heat transfer applications, where turbulent flows are often encountered. Understanding Y Plus in turbulent flows is instrumental in predicting the rate of heat transfer and optimizing heat exchanger designs in industrial processes. In essence, Y Plus acts as a bridge between the orderly world of the viscous sub-layer and the chaotic realm of the outer layer, making it a valuable tool in the realm of fluid mechanics.
Factors Affecting Y Plus
Y Plus is not a static parameter; its value varies depending on several factors that influence fluid behavior near solid boundaries. These factors play a critical role in determining the accuracy of Y Plus calculations and the subsequent understanding of boundary layer flows. To obtain reliable Y Plus values, engineers and scientists must consider the following influential factors:
- Reynolds Number: The Reynolds number is a dimensionless parameter used to predict the flow regime. It directly affects Y Plus, as it determines whether the flow is laminar or turbulent. At higher Reynolds numbers, the flow tends to be turbulent, and Y Plus becomes more critical in characterizing the boundary layer.
- Surface Roughness: The roughness of the solid boundary impacts the behavior of the boundary layer and, consequently, Y Plus. A rough surface disrupts the flow, creating changes in the boundary layer thickness and characteristics. Engineers must account for surface roughness when calculating Y Plus in real-world applications.
- Flow Type: Whether the flow is laminar or turbulent significantly affects Y Plus. In laminar flows, the boundary layer is more predictable, while in turbulent flows, it becomes more complex. Y Plus calculations should be tailored to the specific flow type under consideration.
Taking these factors into account is essential for accurate Y Plus calculations and, by extension, for understanding the nature of the boundary layer and its impact on various engineering applications. Engineers must adapt their approaches and simulations to the specific conditions of the problem they are trying to solve, making Y Plus a versatile and adaptable tool in the field of fluid mechanics.
Y Plus in Practical Applications
The concept of Y Plus isn’t confined to the realms of theoretical fluid mechanics; it finds extensive application in practical engineering scenarios across diverse industries. Its utility extends to areas such as aerospace, automotive engineering, and civil engineering, where it plays a critical role in the optimization of various design parameters. In the field of aerodynamics, Y Plus is harnessed to design and optimize airfoils, wings, and other aerodynamic surfaces. Engineers seek to reduce drag, improve lift, and enhance overall aerodynamic performance, making Y Plus a fundamental tool in the development of efficient aircraft and spacecraft.
The automotive industry, on the other hand, relies on Y Plus to enhance the performance and fuel efficiency of vehicles. By controlling the boundary layer near the vehicle’s surface, engineers can reduce drag, thereby improving fuel economy. Civil engineers, too, leverage Y Plus to design building shapes that minimize wind-induced forces, making structures more stable and safe in diverse environmental conditions. From aviation to ground transportation to civil infrastructure, the practical applications of Y Plus are both wide-ranging and pivotal.
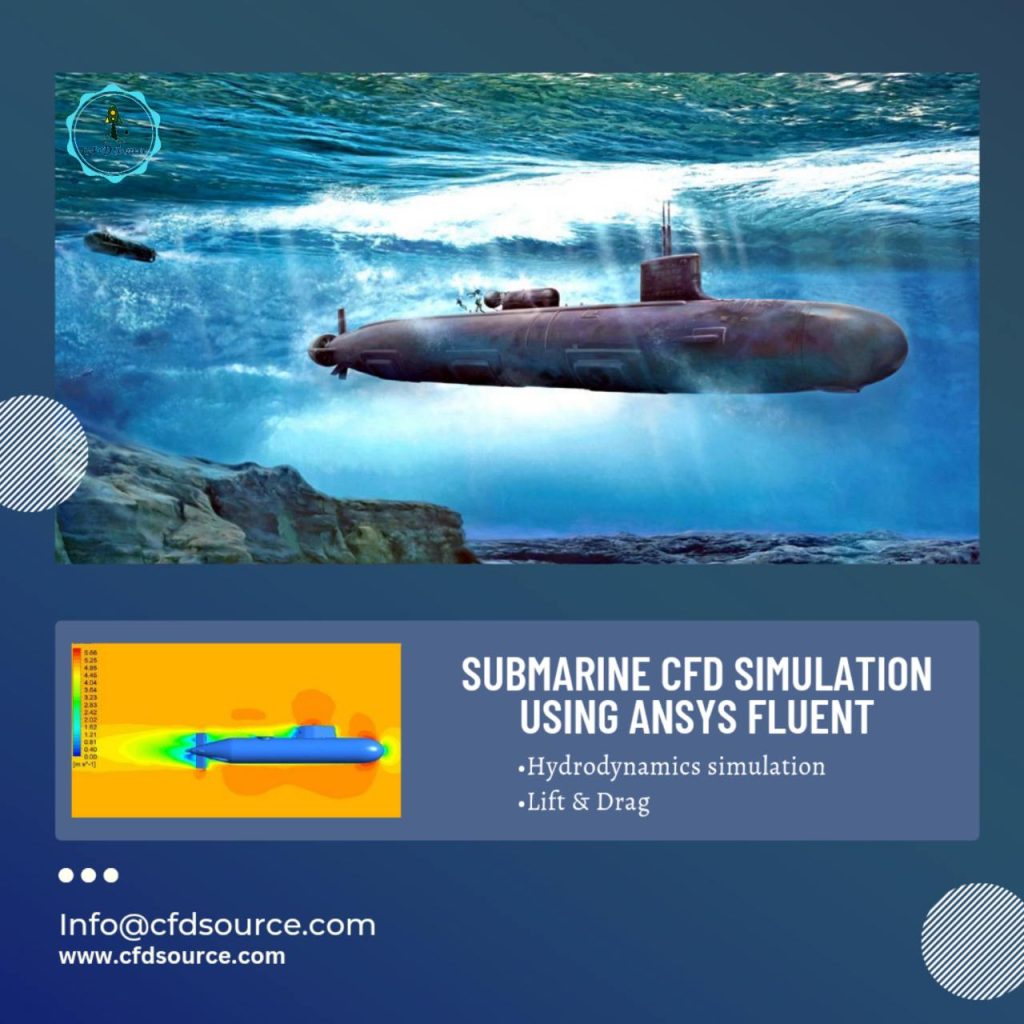
Challenges in Y Plus Calculation
While Y Plus serves as a valuable parameter in fluid mechanics and engineering applications, it’s not without its challenges, particularly in terms of accurate calculation. Several factors contribute to the complexity of Y Plus determination. First and foremost, complex geometries pose a significant challenge. In real-world scenarios, the shapes of objects and surfaces are rarely simple, and modeling these shapes accurately in computational fluid dynamics (CFD) simulations can be intricate. Meshing and boundary layer refinement become more complex in such cases. Additionally, turbulent flows, which often require precise Y Plus calculations, can introduce a level of complexity that demands advanced modeling techniques.
Careful consideration of grid refinement and solution accuracy is essential to ensure reliable results. Furthermore, boundary conditions and the choice of turbulence models have a substantial impact on Y Plus calculations. Engineers need to carefully select appropriate boundary conditions and turbulence models that match the characteristics of the flow. Inaccurate choices can lead to flawed results. Finally, experimental validation is often necessary to verify the accuracy of Y Plus calculations, adding an additional layer of complexity to the process. These challenges underscore the importance of expert knowledge and attention to detail when working with Y Plus, especially in the context of complex and turbulent flows.
Y Plus and Boundary Layer Control
The concept of Y Plus isn’t limited to understanding and characterizing boundary layers; it also serves as a tool for controlling boundary layer flow. Engineers harness the information derived from Y Plus to make specific modifications to the solid boundary or surface, thus influencing the flow characteristics. One of the primary goals of boundary layer control is to optimize the performance of various engineering systems, particularly in scenarios where reducing drag, enhancing lift, or improving heat transfer is paramount. To achieve these objectives, engineers may opt to manipulate the surface roughness or incorporate features that interact with the boundary layer flow.
For instance, in aviation, engineers design airfoil surfaces with precisely controlled roughness to influence the boundary layer. This can lead to reduced drag and enhanced lift, which are crucial for aircraft efficiency. Additionally, innovative designs such as vortex generators and boundary layer trips are implemented on wings and airfoils to control the boundary layer flow and enhance overall aerodynamic performance. Similarly, in heat exchangers, a well-controlled boundary layer is vital to maximize heat transfer efficiency. Engineers use fin arrays and other surface enhancements to influence the flow characteristics, ultimately improving heat exchanger performance.
Y Plus is an indispensable tool in this process because it provides the critical information needed to make informed decisions regarding boundary layer control. By knowing the nature of the boundary layer and the specific Y Plus values at different locations on the surface, engineers can tailor their modifications to achieve the desired outcome. This precise control not only optimizes performance but can also lead to significant energy savings in various engineering applications.
Conclusion
What is Y Plus (y+)? In conclusion, Y Plus, a dimensionless parameter in fluid mechanics, serves as a fundamental tool in the analysis and optimization of fluid flows near solid surfaces. Its significance lies in its ability to characterize boundary layers, distinguish between laminar and turbulent flows, and provide critical insights into complex fluid behaviors. As an essential component of computational fluid dynamics (CFD) simulations, Y Plus has far-reaching practical applications in industries such as aerospace, automotive engineering, and civil engineering. Its influence extends to optimizing aerodynamic designs, enhancing fuel efficiency, and improving structural stability.
However, working with Y Plus is not without its challenges. Accurate calculation demands consideration of complex geometries, turbulence modeling, boundary conditions, and often requires experimental validation. Nevertheless, these challenges are worth overcoming, given the substantial benefits that Y Plus can bring to engineering applications.
In the world of fluid dynamics, Y Plus remains an indispensable tool for optimizing performance and efficiency, making it a vital component in the toolkit of engineers and scientists striving to make advancements in their respective fields. With the right knowledge and approach, Y Plus continues to push the boundaries of what is possible in fluid mechanics, offering valuable insights into the complex world of boundary layer flows.